Tool and Process Monitoring System
GEMCPU
GEMCPU is an autonomous intelligent tool and process monitoring system providing an automatic real-time image of a current production process. Safe and reliable metal cutting processes are essential for economically efficient production.
GEMCPU‘s multi-criteria monitoring strategy adapts automatically to machining processes. This means that the system records all relevant signals and sets the limits based on special algorithms. During the following cutting cycles GEMCPU adjusts the automatic limits. Experts can change and manually fix the limits. The modular system can be easily integrated into machine and network structures. Via fieldbus interfaces data is exchanged with CNC controls.
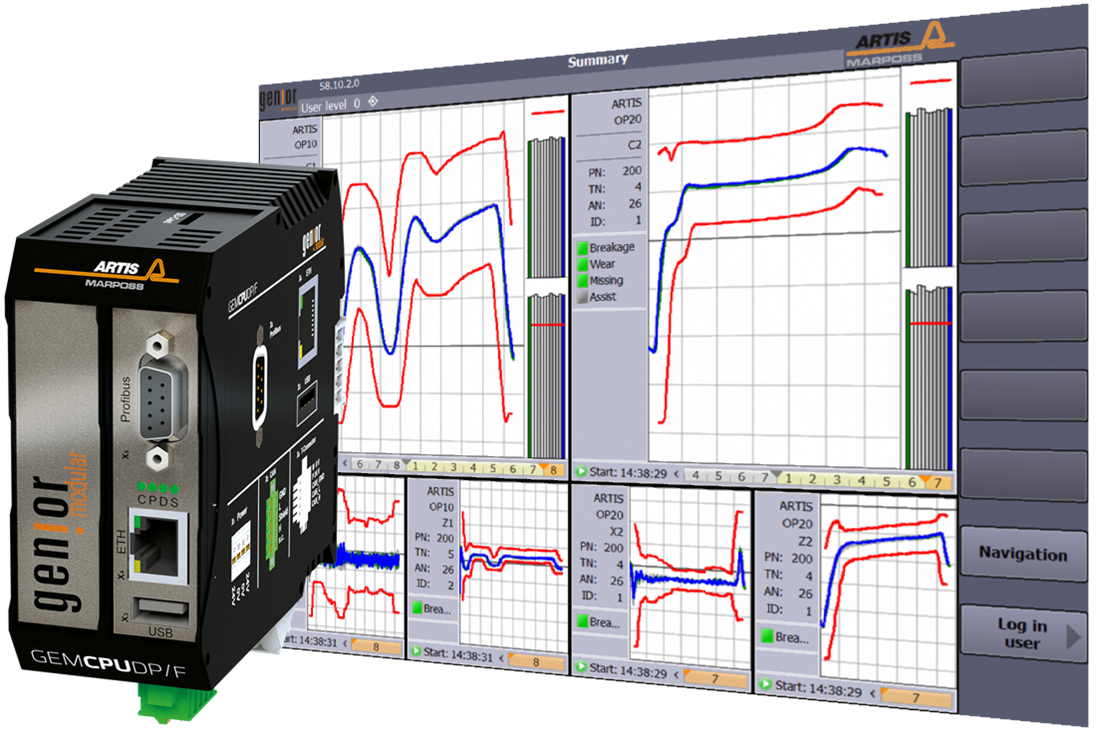
The modular system makes use of all relevant process signals and data from machine tools. It reacts in real-time after an event occurs. The system captures the measurement data digitally via fieldbus interface or via sensors and then evaluates the data based on multiple criteria and visualizes the processes in a transparent way. Trend or alarm reports support the users to optimize processes and allow to produce much more efficiently.
In addition to the described functions, data (BIG DATA) are collected and converted into information (SMART DATA) which can be stored locally or on network devices for further evaluations like analysis, trend curves, statistics and reports.
The option Adaptive Control adjusts the set feed rate of the cutting cycle, so that the effective force of the tool is as stable as possible. A reduction of cycle time can be the result of this feed rate optimization.
GEMCPU is also capable of detecting the wear of a brushing tool and thus automatically adjusting the feed axis.
The modularity of the system is one of the characteristic features needed to adapt the monitoring system to dedicated systems and machines. It is easy to integrate additional function modules, for example GEMTP, GEMGP and GEMVM.
The MultiView process visualization gives an overview about all parallel monitoring processes. Additionally, zooming, back tracing and filtering of different cycles is possible as well. Via Plug-ins (APPs) additional and/or customized functions can be activated, like csv-export, trend curves or statistics.
The option „FINGERPRINT“ (condition monitoring) shows variations in vibration and torque. An alarm will be given when these changes are still marginal and reach set limits to enable status-oriented maintenance.
- Modular/scalable: Economical solution, even for simple applications
- Efficient: Parallel to the process, up to 16 real-time measuring signals in up to 10 NC channels (partly optional) can be acquired.
- Automatic adjustment of alarm limits: makes tedious adjustment to machines or readjustment of limits practically unnecessary - manual adjustments can be made as required or may necessary for special applications
- Optimum use of tool lifetime: Based on the performance data or vibrations, optimum tool utilization can be achieved by evaluating the set wear limit (optional)
- Analysis functions: Process signals are recorded and can be monitored online or offline
- Blackbox: an event recorder records limit violations with time stamping
- Data processing: Plug-ins (APPs) for error evaluation, for trends and for CSV data-output included
- Overview for quick decisions: the online visualization MULTIVIEW shows all relevant signals and their deviations
- Adjustments: the password-protected EXPERT MODE allows many individual adjustments
- Up to 16 real-time measuring signals distributed in up to 10 channels (optional)
- Adjusts the alarm levels automatically if possible
- Optimum tool utilization by evaluating the set wear limits (optional)
- Modular structure, scalable system adaptable to most machine types, easy to install on DIN rail
- Additional analytic functionalities, data processing for Industrial Internet of Things
- Networking with other systems
- MultiView and PlugIn-technology to support users in process optimization
- Expert Mode for individual adjustments
- OPTIONS: tool wear, adaptive control AC, machine condition monitoring, "Fingerprint", data import (data interface for C-THRU4.0)
GEMCPUDP/F: processor unit with Profibus and for FOCAS (FANUC controls)
GEMCPUPN: processor unit with ProfiNET
GEMCPUS828: Evaluation unit for SIEMENS SINUMERIK 828 controls
Various modules:
GEMIO01: Input/Output module for parallel wiring
GEMTP: True power module to connect up to 3 hall sensors
GEMFM01: Force module to connect various Artis/Marposs force sensors (1 sensor per module)
GEMAM01: Acoustic Emission module to connect AE sensors (1 sensor per module)
GEMVM: Vibration module to connect and acceleration and temperature sensors
GEMCMV: Module for the connection of vibration sensors. GEMCMV protects the machine against dynamic collisions and additionally transmits the signals for process monitoring.
GEMCMS: Module for the connection of vibration sensors. GEMCMS protects the machine against quasistatic and dynamic collisions and additionally transmits the signals for process monitoring.
GEMTF01: Torque module to connect DDU torque sensor technology (1 sensor per module)
Via the Ethernet connection, the visualization can be performed on a PC like Artis operator panel IPC7 or IPC10, on any Windows or Linux based PC in the machine or network
BROCHURES AND MANUALS
Brochure | Data Sheet | |
---|---|---|
English |
SMART MONITORING SOLUTION: (7.88MB)
|
GEMAM-01: (1.45MB)
GEMIO-01: (1.29MB) GEMTF-01: (1.43MB) GEMCPU MONITORING MODULES: (1.72MB) |
Italian | - |
GEMCPU MONITORING MODULES: (1.98MB)
|
German |
SMART MONITORING SOLUTION: (8.11MB)
|
GEMAM-01: (1.45MB)
GEMIO-01: (1.30MB) GEMTF-01: (1.43MB) GEMCPU MONITORING MODULES: (1.85MB) |
Japanese | - |
GEMCPU MONITORING MODULES: (0.98MB)
GEMIO-01: (569.67kB) GEMTF-01: (629.26kB) |
Simplified Chinese | - |
GEMCPU MONITORING MODULES: (1.30MB)
|