Coolant Flow Sensors
FLS
The FLS flowmeter measures the amount of cooling lubricant used for internal and external tool cooling. The sensor can be installed at different positions in the piping system of the machine tool. Various Artis FLS models are available for the required flow rate and pressure stability (see versions below). The measuring signal of the precise sensors is evaluated by an Artis monitoring system (CTM or GENIOR MODULAR) to monitor the active flow within the set limits and to set defined alarms in case of deviations.
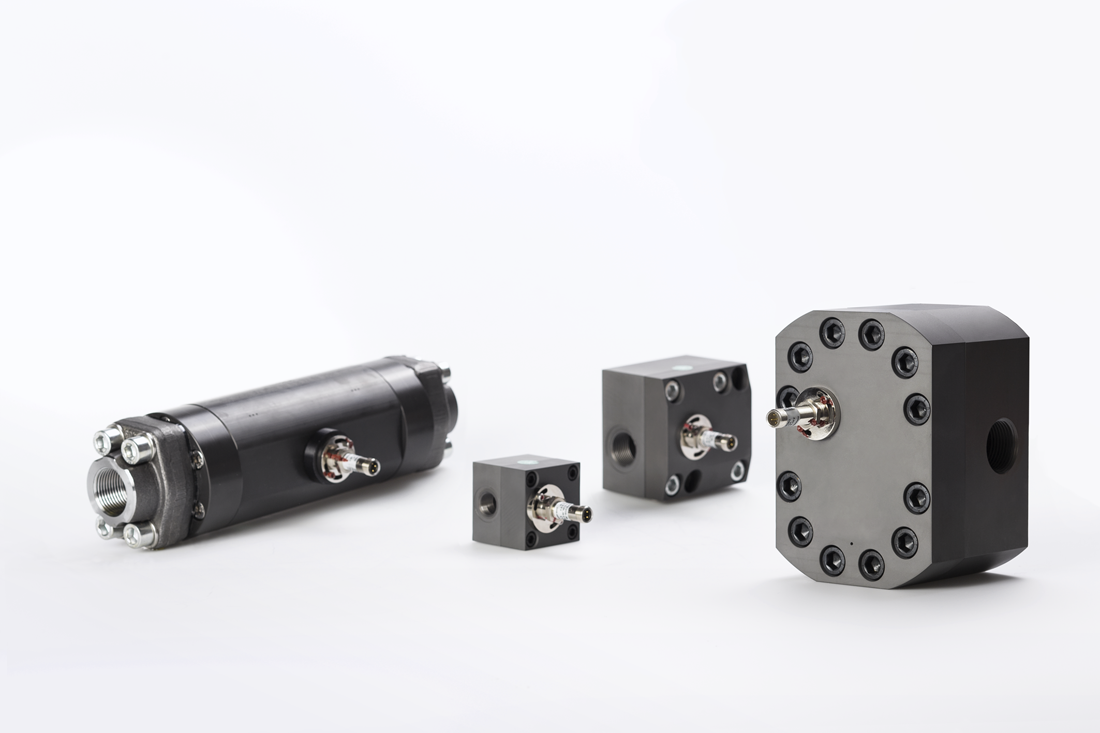
The cooling lubricant is a fluid for cooling and lubricating the tool. It can be used to prevent overheating of the workpiece or the tool during machining (and resulting damage up to destroying it). Lubrication contributes to effective machining and chips are flushed away. The effect of the coolant is closely linked to the flow rate. If the optimized use of the cooling lubricant is disturbed, quality defects are possible.
Artis FLS sensors quickly detect a malfunction of the process component so that early intervention avoids associated follow-up costs, e.g. caused by scrap parts or increased tool wear. Especially in deep hole drilling processes with small shank diameters, this type of monitoring reliably detects tool wear or breakage as well as chip clamping. Thanks to intelligent strategies, Artis evaluation systems solve problems with chip jams without requiring operator intervention.
- Frequent sampling rate
- Temperature stability
- High repeatability
- Able to measure very low volume changes (example – internal cooling of deep-hole drills)
- Integration into the Artis tool and process monitoring systems CTM (CFM-4) and GENIOR MODULAR (GEMGP)
- Wide variety of possible flow rates and pressures
- IP 67 protection degree
Artis FLS cooling lubricant flow sensors are suitable for viscous liquids and self-lubricating media (soaps, pastes, emulsions with non-abrasive character) and have a voltage signal output from 0 to 10 V.
- FLS-2 for pressure up to max. 200 bar and maximum coolant flow of 0.02 to 2 l/min
- FLS-6 for pressure up to max. 200 bar and maximum coolant flow of 0.1 to 6 l/min
- FLS-50 for pressure up to max. 200 bar and maximum coolant flow of 0.5 to 50 l/min
- FLS-60-400 for pressure up to max. 400 bar and maximum coolant flow of 0.3 to 60 l/min
- FLS-150-100 for pressure up to max.100 bar and maximum coolant flow of 3 to 150 l/min
- FLS-150-350 for pressure up to max. 350 bar and maximum coolant flow of 1.4 to 140 l/min
