Thickness measurement of the insulation layer on magnet wire
Several researches showed that there are significant advantages in using flat wire hairpin windings in some types of motors. The advantage is a much higher copper slot fill factor reducing heat and improving torque and power density, which ultimately can reduce the motor size for EV application.
However, in order to obtain this performance improvement, it is necessary to guarantee an adequate quality level of the component and that its production process is perfectly under control.
A perfect control of the thickness of the insulation layer is generally one of the critical parameters in the production of magnet wire, and in particular when it comes to the flat wire used for the production of hairpins. The constancy and uniformity of this thickness is in fact related not only to the quality and effectiveness of the electrical insulation, but can also influence the subsequent bending process in the production of the hairpin.
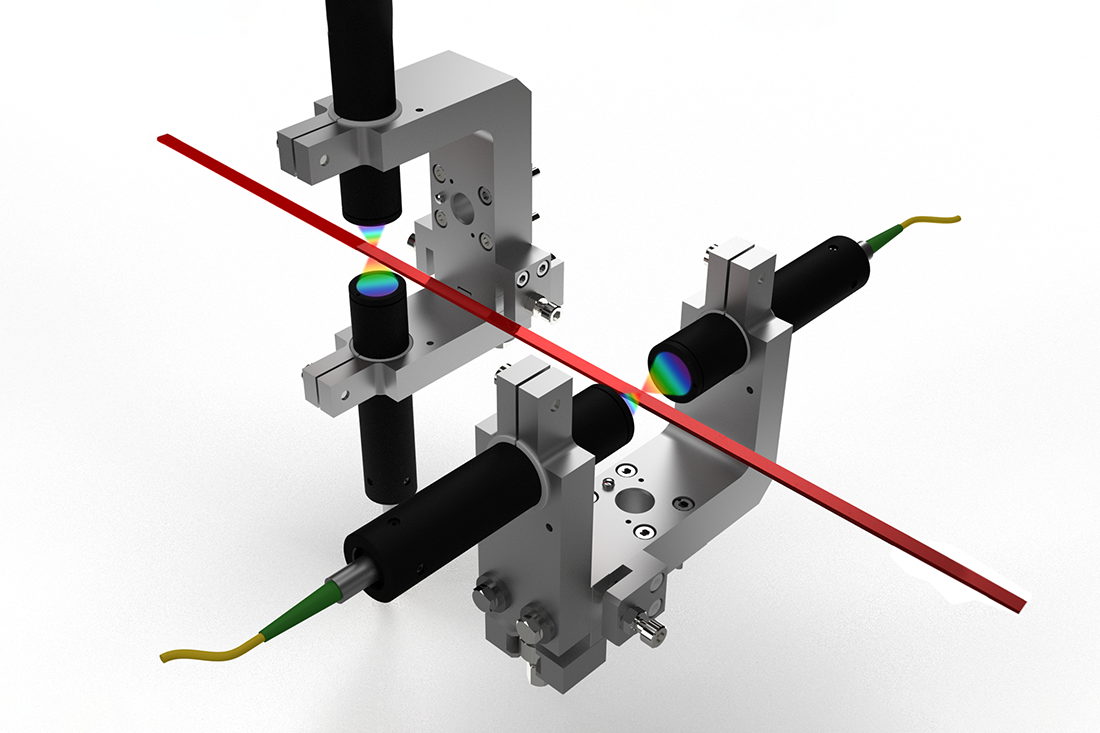
Control of enameled wire
Electrical insulation on magnet wire is often achieved by surface coating of enamels such as PI (polyimide) or PAI (polyamide-imide).
These materials are usually partially transparent to white light and their thickness can therefore be measured using confocal chromatic technology.
Marposs STIL offers a wide range of electronics and optical sensors based on confocal chromatic technology that can be used for this purpose.
Control of PEEK extruded flat wire
With the need to improve performance on components for the automotive sector, the use of extruded PEEK flat wire is increasingly widespread, a material capable of ensuring better thermal and electrical behaviour, and which can be produced with a lower environmental impact.
The PEEK coatings most frequently used for this purpose are normally opaque and cannot be controlled with confocal technologies. However, these materials are usually transparent in the Near-infrared (NIR) wavelength band (0.75 – 1.4 µm) and their thickness can be measured with interferometric sensors. The same type of sensors is then clearly also able to measure the thickness of enamels such as PI/PAI.
The Marposs Horizon interferometric product line is therefore the ideal solution for measuring thin thicknesses of this type of coatings.
Off-line thickness measurement
One single sensor (confocal or interferometric, depending on the specific needs) assembled into a dedicated gauging tool can be used for laboratory analysis, with off-line measurement of the enamel thickness on samples of the wire taken from production. The enamel coating or PEEK extrusion operations are usually slow trend processes and they can be controlled through a periodical off-line check of samples.
-
In-line thickness control
In-line sensors can be integrated for continuous control during production. A "fork" configuration, with two facing sensors, allows continuous measurements of the thickness of the insulation layer on two opposite sides, together with the total thickness of the wire. Two forks positioned at 90° can be used to measure all 4 sides of the flat magnet wire.
The same technologies can also be used to check the quality of the wire in a subsequent operation in the production of hairpins, where the control of thickness and symmetry of the insulating layer is essential to guarantee the correct execution and stability of the bending process.
- Conformity certification of the thickness and symmetry of the insulating layer on flat magnet wire
- Non contact gauging technology
- Control of the enamel coating or PEEK extrusion process
- Prevention of issues due to out of control springback after hairpin bending
- Measurement of enamel thickness with confocal sensors
- Measurement of the PEEK thickness with NIR interferometer
Defined according to customer’s requirements