Dickenmessung der Isolierschicht an Magnetdrähten
Verschiedene Studien haben gezeigt, dass es deutliche Vorteile hat, wenn für einige Arten von Motoren Flachdraht-Hairpin-Wicklungen verwendet werden. Der Vorteil liegt in dem viel höheren Füllfaktor der Kupfernuten. Dadurch wird weniger Hitze erzeugt und das Drehmoment sowie die Leistungsdichte sind höher. Im Endeffekt kann so die Größe der Motoren für Elektrofahrzeuge verringert werden.
Um diese Leistungssteigerung zu erreichen, ist es jedoch notwendig, die entsprechende Qualität der Komponente zu garantieren. Außerdem muss der Herstellungsprozess stets perfekt unter Kontrolle gehalten werden.
Die perfekte Kontrolle über die Dicke der Isolierschicht ist im Allgemeinen einer der kritischen Parameter bei der Fertigung von Magnetdrähten, vor allem dann, wenn es sich um Flachdrähte zur Herstellung von Hairpins handelt. Die Gleichförmigkeit und Gleichmäßigkeit dieser Dicke bestimmt nicht nur die Qualität und Wirksamkeit der elektrischen Isolierung, sondern kann später auch den Biegevorgang bei der Herstellung der Hairpins.
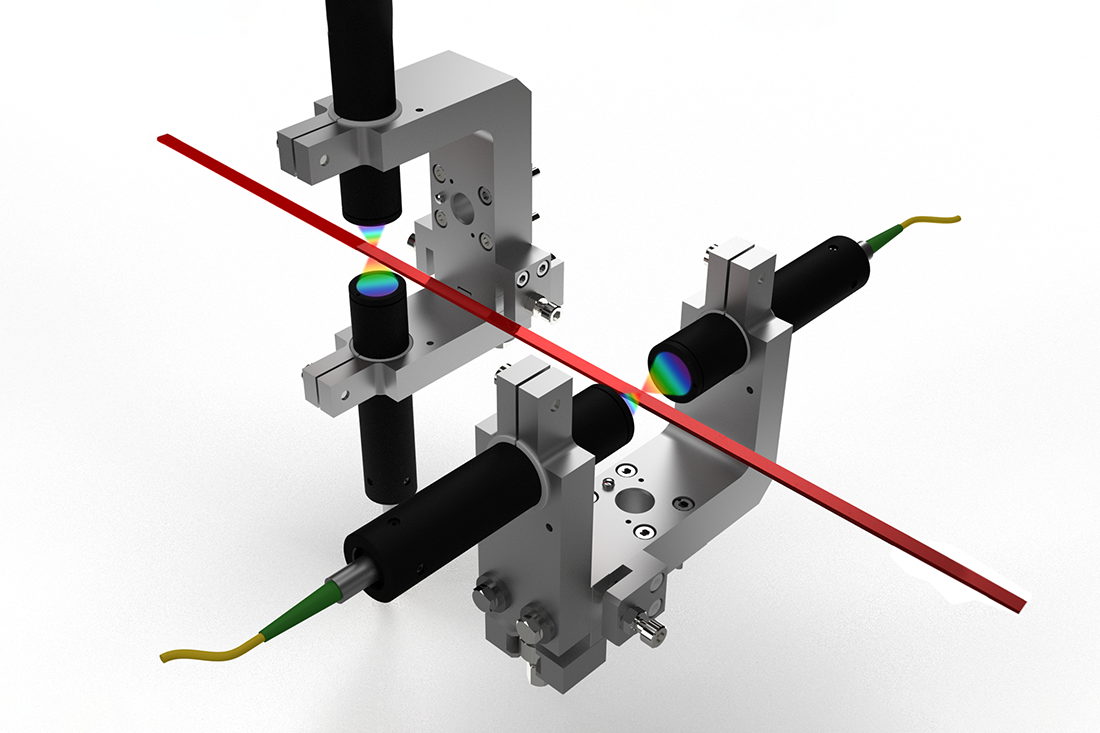
Kontrolle von lackierten Drähten
Die elektrische Isolierung von Magnetdrähten wird oft durch Lackierung der Oberfläche, etwa mit PI (Polyimiden) oder PAI (Polyamidimiden), erreicht.
Diese Stoffe sind normalerweise teilweise für Weißlicht transparent. Dadurch kann ihre Dicke mithilfe der chromatisch-konfokalen Technologie gemessen werden.
Marposs STIL bietet eine große Bandbreite an elektronischen und optischen Sensoren mit chromatisch-konfokaler Messtechnik, die für diesen Zweck verwendet werden können.
Kontrolle von extrudierten PEEK-Flachdrähten
Durch den Bedarf der Automobilindustrie, die Leistung der einzelnen Komponenten immer weiter zu verbessern, hat sich die Verwendung von extrudierten PEEK-Flachdrähten mehr und mehr verbreitet. Dieses Material bietet bessere thermische und elektrische Merkmale und kann mit einer niedrigeren Umweltbelastung hergestellt werden.
PEEK-Beschichtungen, die zu diesem Zweck meistens verwendet werden, sind normalerweise opak und können nicht mit konfokalen Technologien überprüft werden. Diese Materialien sind jedoch normalerweise im Nahinfrarot-Wellenlängenbereich (NIR) (0,75 – 1,4 µm) transparent und ihre Dicke kann mit interferometrischen Sensoren gemessen werden. Diese Sensoren sind außerdem natürlich dazu imstande, die Dicke von Lacken wie PI/PAI zu messen.
Die interferometrische Produktreihe Marposs Horizon ist somit die ideale Löschung zur Messung der Dicke solcher Beschichtungen.
Offline-Dickenmessung
Ein einzelner Sensor (je nach Bedarf konfokal oder interferometrisch), der in ein entsprechendes Messinstrument eingebaut ist, kann für Laboranalysen zur Messung der Lackdicke an Drahtstichproben verwendet werden, die aus der Fertigung entnommen werden. Bei der Lackbeschichtung oder der PEEK-Extrudierung handelt es sich normalerweise um Prozesse mit langsamen Trends, die durch die regelmäßige Überprüfung von Stichproben außerhalb der Fertigungslinie unter Kontrolle gehalten werden können.
-
Inline-Dickenmessung
Zur ständigen Kontrolle während der Fertigung können Inline-Sensoren integriert werden. Eine „Gabelkonfiguration“mit zwei Sensoren, die einander gegenüber liegen, erlaubt eine durchgehende Dickenmessung der Isolierschicht auf zwei Seiten zusammen mit der Messung der Gesamtdicke des Drahts. Zwei Gabeln, die in einem 90-Grad-Winkel angebracht sind, können dazu verwendet werden, alle 4 Seiten eines flachen Magnetdraht zu vermessen.
Diese Technologien können auch dazu genutzt werden, die Drahtqualität in späteren Schritten der Hairpin-Fertigung zu überprüfen, bei denen die Kontrolle der Dicke und Symmetrie der Isolierschicht von wesentlicher Bedeutung ist, um die korrekte Ausführung und Stabilität des Biegeprozesses zu gewährleisten.
- Konformitätszertifizierung der Dicke und Symmetrie der Isolierschicht bei flachen Magnetdrähten
- Berührungslose Messtechnik
- Kontrolle der Lackschicht oder der PEEK-Extrudierung
- Vorbeugung vor Problemen durch unkontrollierte Rückfederung nach dem Biegen der Hairpins
- Messung der Lackdicke mit konfokalen Sensoren
- Messung der PEEK-Dicke mit NIR-Interferometer
Genau auf die Anforderungen des Kunden zugeschnitten