Assembly Lines For Power Electronics And Battery Chargers
Marposs provides flexible solutions for the complete assembly of power electronic units,XBattery Chargers and Inverters. Different configurations, including manual or fully automatic assembly operations, can be provided, according to customer’s specifications.
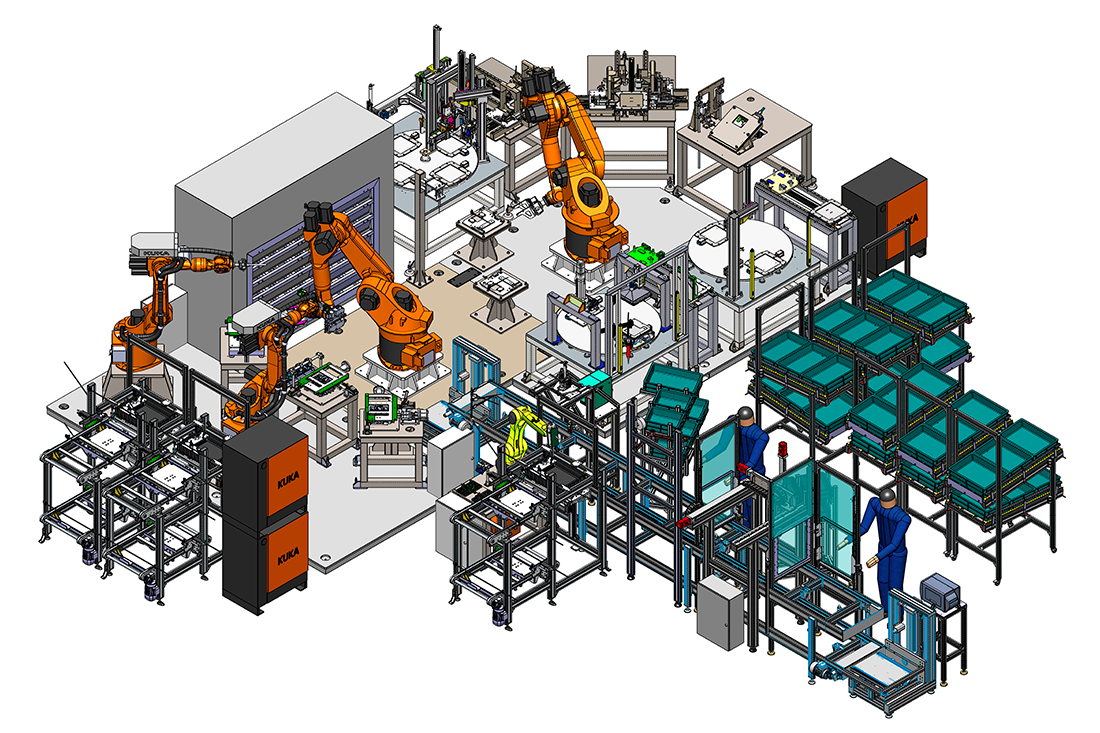
Automatic line for assembling all the components of a Battery Charger for electric vehicles. The process is split in 2 different phases:
- In the first one, the cover with electronic boards are assembled.
- In the second one, the assembly of the bottom side is completed. Both sides are cleaned with ionized air before performing leak testing and electrical testing.
PHASE #1
All the operations are performed by operators in no.3 manual stations.
- The cover is collected by the operator and ionized in a segregated area.
- The main power connectors are assembled in the following manual station.
- The electric boards are picked by operator and screwed.
During all activities, operators are guided by a panel PC and the components are tracked by data matrix reading.
PHASE #2
During the second phase, the operations are also split in 2 main areas:
- In the first one, bottom components are processed by operators and handled by a chain conveyor.
- In the second one, bottom covers are handled by anthropomorphic robots and assembled by automatic stations and turning tables.
First area – handling by chain conveyor
The bottom case, completed with gaskets, are picked by operators and put on pallets, handled by chain conveyor.
- In the first station of conveyor, the bottom cover is cleaned with ionized air in a segregated area.
- In the second one, a camera system handled by electrical manipulator, check the correct position and integrity of gaskets.
- The third one, is dedicated to the water connectors, that are screwed by operators; the screws are supplied one by one, automatically.
- On the fourth one, the electronic boards are placed by operators and screwed. Screws are automatically supplied one by one, also in this station.
All components, picked for the assembly process, are traced by Data Matrix reading. Operators are guided by panel PC during the whole operations.
Second area – handling by anthropomorphic robots
The robot collects the bottom case for the assembly process.
- On the first operation, the cooling circuit is checked by air leak testing (pressure 2,5 bar – 15”).
- On the second one, electromagnetic coils are picked by a second robot and placed inside the case: the bottom cover has been previously located on the second working station by the first robot.
- The third one is dedicated to the resining process: the case is pre-heated before fixing internal components and afterwards filled by a resin dispenser.
- On the fourth one, the case is left by the first robot inside the oven for resin maturation.
In the last phases, the process is in charge to the turning tables.
The first turning table receives the case from the robot and it will perform the following activities:
- The bottom side of the cover is cleaned by ionized air.
- It is assembled with a second electronic board.
- It is screwed by operator and checked by camera.
- At the end of the whole turning table rotation, the case is given back to the robot.
In the final phase, the upper case is manually collected from a storage area, assembled and screwed. After that, the process will be completed by the second and third turning table with the operations described here below:
- The case is left on the second turning table for the last air leak test (0,20 bar – 15”).
- It is tested by electrical tester and, if the test is positive, the case will be marked by laser.
- The last valve is assembled on the third turning table before being unloaded by operator.
Manual Stations
- High efficiency = 90%.
- High flexibility of assembly processes: the manual stations allows a modification and/or an upgrade of assembly process with quick and easy mechanical improvements.
- Easy operators exchange: the panel PC drives operators during the manual operations. It allows the maximum efficiency also for new operators.
Automatic Stations
- High efficiency = 90%.
- High automation process: all critical operations are in charge of the automatic device, leaving easy assembly processes for the operators.
- Easy operators exchange: the panel PC drives operators during the manual operations. It allows for maximum efficiency, for new operators as well.
- Defined according to customer’s specifications
Manual Stations
Cycle time at 100% | 239 sec |
Cycle time at 90% | 262,9 sec |
Production |
15,6 parts / hour |
Efficiency | 90% |
Automatic Stations
Cycle time at 100% | 210 sec |
Cycle time at 90% | 233 sec |
Production | 17 parts / hour |
Efficiency | 90% |