Montagelinien für Leistungselektronik und Akku-Ladegeräte
Marposs bietet flexible Lösungen für die komplette Montage von Leistungselektroniken wie zum Beispiel Akku-Ladegeräten und Invertern. Verschiedene Konfigurationen, die sowohl manuelle als auch vollautomatischer Montagevorgänge einschließen können, werden genau auf die Anforderungen der Kunden zugeschnitten.
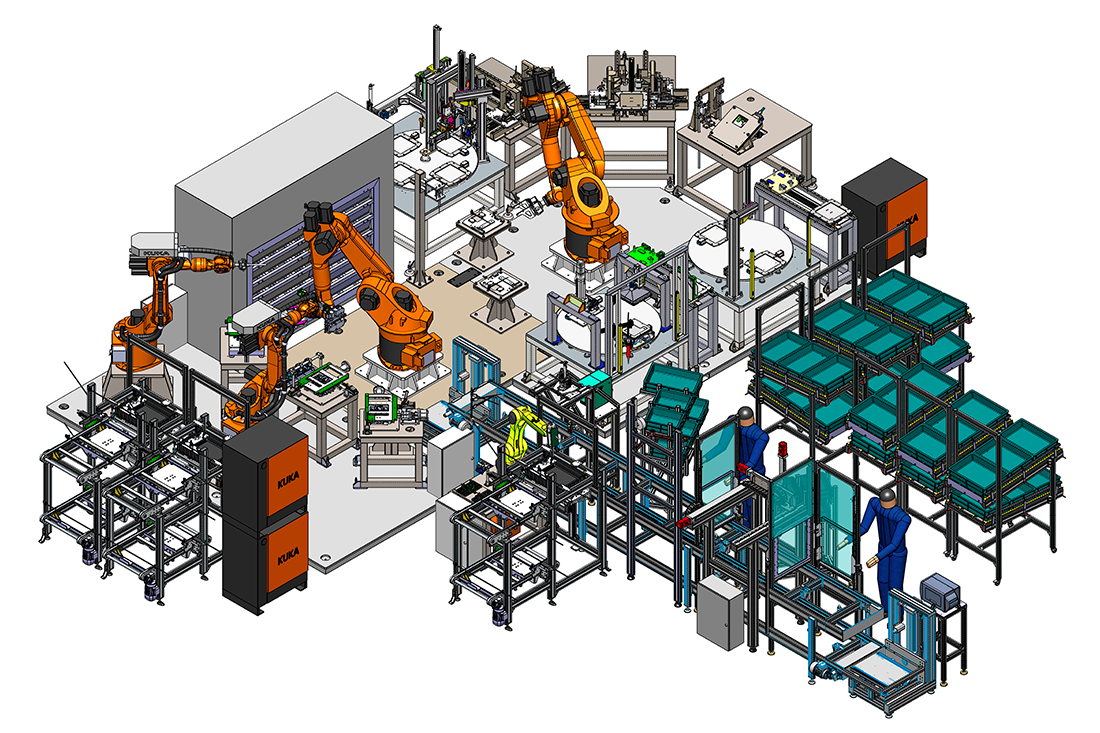
Automatische Linie zur Montage aller Komponenten eines Akku-Ladegeräts für Elektrofahrzeuge. Der Prozess ist in zwei Phasen aufgeteilt:
- In der ersten wird die Abdeckung mit elektronischen Platinen montiert.
- In der zweiten erfolgt die Montage des Bodens. Beide Seiten werden mit ionisierter Luft gereinigt, bevor die Dichtheitsprüfung und die elektrische Prüfung vorgenommen werden.
PHASE #1
Alle Tätigkeiten werden von Bedienern in 3 manuellen Stationen ausgeführt.
- Die Abdeckung wird vom Bediener entnommen und in einem abgetrennten Bereich ionisiert.
- In der folgenden manuellen Station werden die Hauptstromanschlüsse montiert.
- Die Platinen werden vom Bediener aufgenommen und verschraubt.
Bei allen diesen Tätigkeiten werden die Bediener über einen Panel PC angeleitet und die Komponenten werden durch Auslesen der Data-Matrix verfolgt.
PHASE #2
In der zweiten Phase sind die Aktivitäten ebenfalls in 2 Hauptbereiche aufgeteilt:
- Im ersten werden die Bodenkomponenten von Bedienern verarbeitet und mit einem Kettenförderer weitergeleitet.
- Im zweiten werden die Bodenabdeckungen von anthropomorphen Robotern entnommen und in automatischen Stationen mit Drehtellern montiert.
Erster Bereich - Handhabung auf Kettenförderer
Der Gehäuseboden, bereits mit Dichtungen versehen, wird von Bedienern aufgenommen und auf Paletten gesetzt, die vom Kettenförderer weitergeleitet werden.
- In der ersten Station des Förderers wird der Gehäuseboden in einem abgetrennten Bereich mit ionisierter Luft gereinigt.
- In der zweiten Station überprüft ein von einem elektrischen Manipulator geführtes Kamerasystem, ob die Dichtungen in der richtigen Position und unversehrt sind.
- In der dritten Station werden die Wasseranschlüsse von Bedienern angeschraubt. Die Schrauben werden automatisch einzeln zugeführt.
- In der vierten Station werden die elektronischen Platinen von den Bedienern eingesetzt und festgeschraubt. Auch in dieser Station werden die Schrauben automatisch einzeln zugeführt.
Alle Komponenten, die für den Montagevorgang aufgenommen werden, werden durch Auslesen der Data-Matrix verfolgt. Bei allen diesen Tätigkeiten werden die Bediener durch einen Panel PC angeleitet.
Zweiter Bereich - Handhabung durch anthropomorphe Roboter
Der Roboter entnimmt den Gehäuseboden für den Montagevorgang.
- Im ersten Arbeitsgang wird der Kühlkreislauf anhand einer Luftleckprüfung (Druck 2,5 bar – 15”) überprüft.
- Im zweiten werden elektromagnetische Spulen von einem zweiten Roboter aufgenommen und in das Gehäuse eingesetzt. Die Bodenabdeckung wird vorher in der zweiten Arbeitsstation vom ersten Roboter erfasst.
- Im dritten Arbeitsgang erfolgt der Harzvorgang: Das Gehäuse wird vorgeheizt, bevor interne Komponenten befestigt werden, und danach mit einer Harz-Ausgabevorrichtung gefüllt.
- Im vierten Arbeitsgang wird das Gehäuse vom ersten Roboter in den Ofen gelegt, damit das Harz aushärten kann.
In den Schlussphasen wird der Prozess mit den Drehtellern fortgeführt.
Der erste Drehteller erhält das Gehäuse vom Roboter und führt folgende Tätigkeiten aus:
- Die Bodenseite der Abdeckung wird mit ionisierter Luft gereinigt.
- Sie wird mit einer zweiten elektronischen Platine ausgestattet.
- Sie wird vom Bediener verschraubt und mit der Kamera überprüft.
- Am Ende der gesamten Drehung des Drehtellers wird das Gehäuse an den Roboter zurückgegeben.
In der letzten Phase wird das Gehäuseoberteil manuell aus einem Lagerbereich entnommen, montiert und verschraubt. Danach wird der Prozess mit dem zweiten und dritten Drehteller abgeschlossen, dabei erfolgen folgende Tätigkeiten:
- Das Gehäuse wird auf dem zweiten Drehteller abgelegt, wo die letzte Luftleckprüfung erfolgt (0,20 bar – 15”).
- Diese Prüfung wird mit einem elektrischen Testgerät durchgeführt. Wenn der Test erfolgreich ist, wird das Gehäuse von einem Laser markiert.
- Das letzte Ventil wird am dritten Drehteller montiert, wonach das Gehäuse vom Bediener entnommen wird.
Manuelle Stationen
- Hohe Effizienz = 90%
- Große Flexibilität bei den Montagevorgängen: Manuelle Stationen erlauben Änderungen und/oder Erneuerungen am Montageprozess durch einfache und schnelle mechanische Verbesserungen.
- Einfacher Bedienerwechsel: Der Panel PC leitet die Bediener bei den manuellen Tätigkeiten an. Dadurch ergibt sich auch für neue Bediener höchste Effizienz.
Automatische Stationen
- Hohe Effizienz = 90%
- Hoch automatisierter Prozess: Alle kritischen Arbeiten sind automatischen Vorrichtungen übertragen, dadurch können die Bediener die bequemeren Montagearbeiten ausführen.
- Einfacher Bedienerwechsel: Der Panel PC leitet die Bediener bei den manuellen Tätigkeiten an. Dadurch wird auch bei neuen Bedienern höchste Effizienz erreicht.
- Genau auf die Spezifikationen des Kunden zugeschnitten
Manuelle Stationen
Zykluszeit bei 100% | 239 s |
Zykluszeit bei 90% | 262,9 s |
Produktion |
15,6 Teile / Stunde |
Effizienz | 90% |
Automatische Stationen
Zykluszeit bei 100% | 210 s |
Zykluszeit bei 90% | 233 s |
Produktion | 17 Teile / Stunde |
Effizienz | 90% |