Technologies -- Non-Destructive Test
Eddy Current (EC) is a family of Non-Destructive Techniques (NDT) used to check superficial quality and material properties of components under test. This is done with no contact between the sensors and the parts to be tested. Furthermore, this can be done without the need for part preparation (deep cleaning, degreasing, etc.)
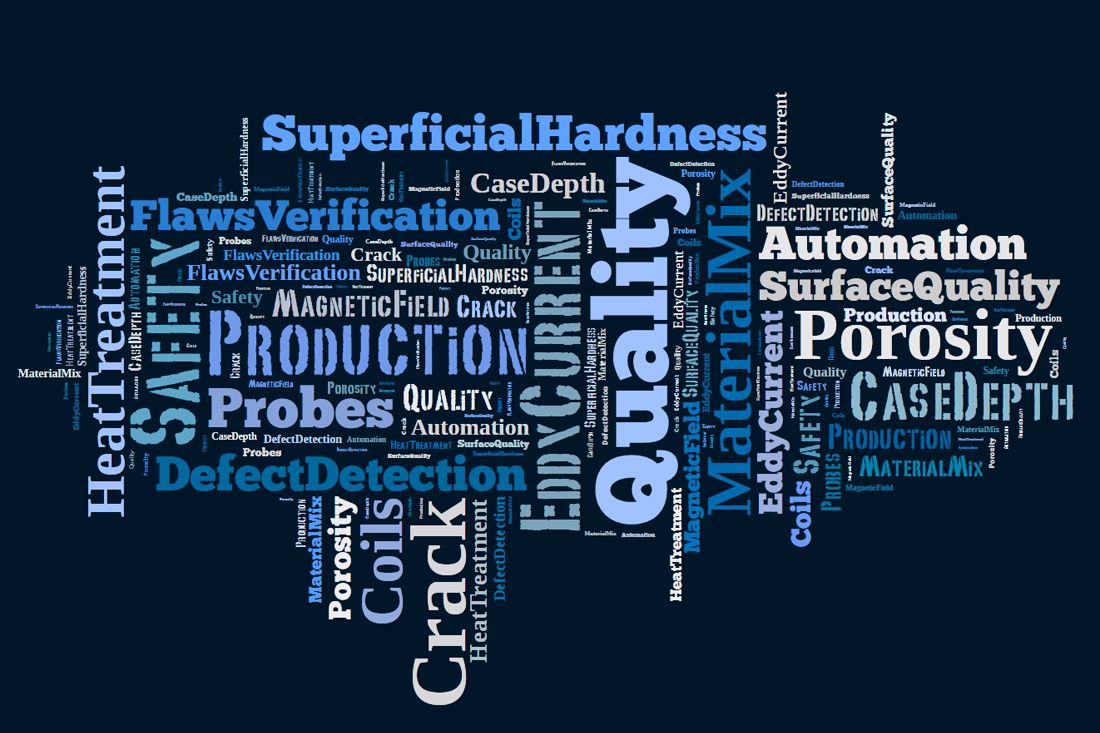
When comparing eddy current inspection to other NDT methods, some of the most important benefits are:
-
It does not require inspection from the operator to determine if a part is good or scrap. Thus, eliminating human error.
-
Surface preparation is not needed (though parts need not be cleaned and dried) allowing eddy current inspection to be fully integrated into the customer’s production lines.
-
No surface damages, or contamination due to contactless characteristic of eddy current inspection.
-
High speed inspection can adapt for the typical rates of production lines.
Nowadays, the quality of the parts produced do not solely relate to their dimensions but also to their safety. Reliability of mechanical components, which may affect the user's safety, is mandatory to guarantee quality production. Non-destructive testing carried out by means of Eddy Current does not affect the usefulness of specimens tested and is a reliable, cost-effective way to ensure the following:
-
The produced parts are not affected by superficial defects such as cracks, porosity, blow holes, etc.
-
The produced parts are manufactured with the proper material.
-
Correct superficial hardness and proper case depth were obtained after the heat treatment process.
-
Presence of thread in tapped holes.
This family of non-destructive tests are based on eddy currents that are small loops of electrical current induced within conductive materials by a time-varying magnetic field.
This magnetic field is produced by an alternating current flowing from a small winding coil, embedded inside the eddy current probe.
This primary magnetic field generates the eddy currents into the conductive materials under test and the eddy currents generate a secondary time-varying magnetic field interacting with one another.
The mutual interaction between the primary and secondary magnetic field is then used to analyze the presence of superficial defects along with the material properties. Furthermore, the presence of superficial defects can change the path of the eddy currents, while different metallurgical characteristics (i.e. superficial hardness or case depth) can be detected. This causes changes of electric conductivity and magnetic permeability of the specimen. These variations are then detected and analyzed to evaluate deviations in respect to proper characteristics of the sample under test.
The mutual interaction between the primary and secondary magnetic field is then used to analyze the presence of superficial defects along with the material properties. Furthermore, the presence of superficial defects can change the path of the eddy currents, while different metallurgical characteristics (i.e. superficial hardness or case depth) can be detected. This causes changes of electric conductivity and magnetic permeability of the specimen. These variations are then detected and analyzed to evaluate deviations in respect to proper characteristics of the sample under test.
Eddy current testing, needs a reciprocal movement between the part to be tested and the eddy current probe. The ease of application involving eddy currents and its contactless characteristics allows the realization of automatic applications to reach 100% production inspection. In addition to this, it has higher testing speeds than any other non-destructive technology allowing a short cycle time.
Most mechanical components, from the simplest screw to the most complex mechanical part, can be tested with eddy currents to detect superficial defects. This is done by automatic or semiautomatic applications to monitor the following:
-
Cracks on crankshaft and camshaft (generated by grinding and or heating process).
-
Blow holes and porosities on engine blocks (caused by casting problems).
-
Cracks on screw caused by hot/cold forming process.
-
Cracks caused by machining and porosities caused by castings defect on brake disk/drums.
-
Cracks on ball pin, CVJ cage, CVT shafts and pulley (generated by the heating and machining process).
- Blow holes and porosities in the alloy rim.