Tool Breakage Detector
TBD
TBD, Tool Breakage Detector, is a system designed by Marposs to check the integrity of tools and guarantee high quality products with few rejects. The mass production of mechanical parts requires very short machining times, consequently the tool checks must be carried as quickly as possible. In less than 1 second TBD is able to check for breakages on solid body concentric tools such as: drill bits, tapping tools and flat and ball end milling cutters.
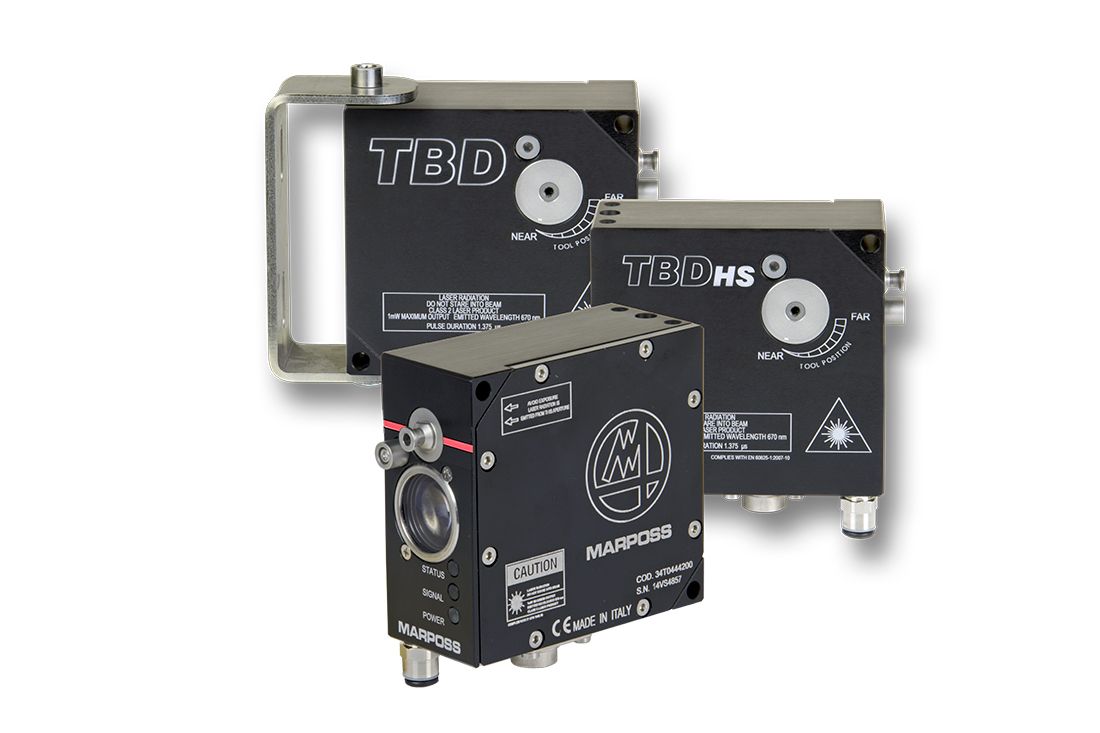
TBD is a contactless system using laser reflection technology. It consists of an emitter that projects the laser beam on the surface of the rotating tool, placed in the check position. Intact tools reflect the signal on the receiver, which is then processed by the internal electronic unit, after being filtered of any interruptions due to droplets of coolant. On the other hand broken tools do not reflect any signal to the TBD, triggering an alarm signal. The laser beam points towards the spindle axis and the check position is identified during the movement towards the magazine, avoiding longer processing times due to more complex positioning operations.
The flexible TBD allows for different operating modes:
- the maximum power setting allows the TBD to detect a tool positioned further away (up to 2 metres), with a standard breakage detection capacity. The “low power” mode, which creates a smaller laser beam, can be used when a lower tolerance is required
- users can choose the signal filtering level. During the tool check cycle droplets of coolant could interrupt the beam or remain on the tip of the tool, altering the reception signal. By setting “Hi Filter”, the TBD software increases the filtering level for a more reliable result. The “Low Filter”, on the other hand, allows the TBD to react more quickly, as the filter threshold is higher
- the most suitable spindle speed range can also be selected
- Fast and reliable breakage detection
- Recognition of a wide range of solid body concentric tools
- Easy to install and wire
- Reduction of rejects and possibility of unsupervised production
- Highly flexible with the various operating options available
For all technical characteristics, please refer to the table in the DOWNLOAD section.
TBD is available in two versions:
- The standard TBD, with an operating range from 200 to 5,000 RPM, designed to be used in most standard applications with machining centres, drilling and tapping machines and where unsupervised productions are required
- TBD HS can check tools rotating at up to 80,000 RPM. It can be used for machining operations that require high finish levels or very fast cycle times. The TBD HS ensures that the high qualitative standard is maintained throughout the machining operation
BROCHURES AND MANUALS
Brochure | User Manual | Installation Manual | |
---|---|---|---|
English |
TBD: (1.97MB)
|
TBD: (1.27MB)
|
TBD: (2.01MB)
|
Italian |
TBD: (1.97MB)
|
TBD: (1.27MB)
|
TBD: (2.07MB)
|
German |
TBD: (1.97MB)
|
TBD: (1.28MB)
|
TBD: (2.09MB)
|
French |
TBD: (1.97MB)
|
TBD: (1.26MB)
|
TBD: (2.14MB)
|
Spanish |
TBD: (1.97MB)
|
TBD: (1.28MB)
|
TBD: (2.12MB)
|
Russian |
TBD: (2.10MB)
|
- | - |
Japanese |
TBD: (2.30MB)
|
- | - |
Korean |
TBD: (4.87MB)
|
- | - |
Simplified Chinese |
TBD: (5.38MB)
|
- | - |
TECHNICAL DOCUMENTS
Tech Specs Table | |
---|---|
English |
(47.92kB)
|
Italian |
(48.59kB)
|
German |
(48.96kB)
|