Rotor Functional Test
The functional testing of rotors varies depending on the type of electric motor and the specific rotor configuration. Factors such as the type of winding, the presence of permanent magnets or short-circuit bars, directly affect the parameters to be verified and the test methodologies to be adopted.
With the E.D.C. product line, Marposs offers a complete range of solutions for the functional testing of any type of rotor, both for in-line and off-line applications, and for analysis and characterization in the laboratory.
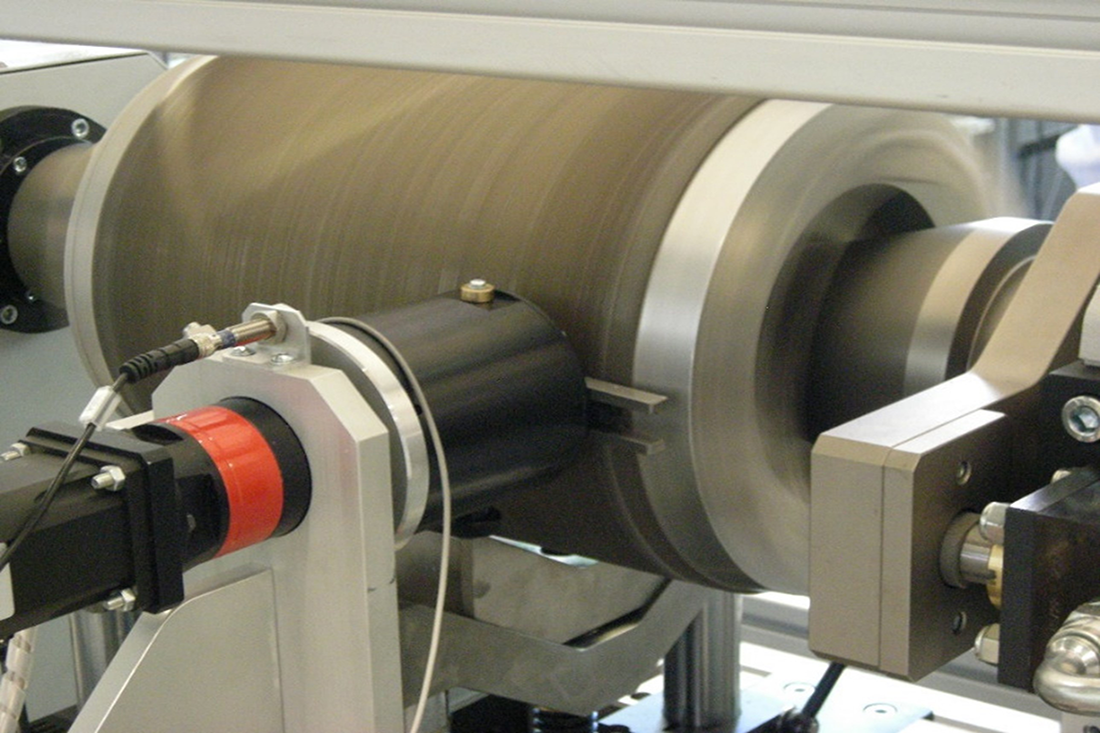
Squirrel cage rotors
In the field of AC asynchronous electric motors, squirrel cage rotors are widely used, with bars obtained directly by die-casting in the lamination stack.
The quality control of this type of rotor is carried out with test stations, both manual and fully automatic for in-line integration, with the aim of detecting any defects in the die-cast bars of the cage.
For this purpose, R-TEST has been developed, an innovative algorithm capable of automatically detecting a wide range of defects that can affect the performance of squirrel cage rotors:
- Broken or damaged bars
- Lack of material in the rotor bars (incomplete material injection, porosity, blowholes)
- Faulty connection or lack of connection between bars and end rings
- Different quality of aluminum alloy and/or laminations
- Short circuit between two or more bars
- Deviation of the bar inclination angle from the axis
- Bar misalignment with respect to the axis
- Problems related to imperfect overlapping of the laminations
The test is performed by rotating the rotor to be tested and using a special probe to generate a magnetic field and detect the signal generated by each bar as it passes through the magnetic field itself. The acquired signal is then processed by the R-TEST algorithm, which is able to selectively identify each of the defects described above.
One of the main strengths of R-TEST is its ability to assign a numerical value to each defect, making it possible to define specific acceptance thresholds for each type of anomaly.
In addition, the RQF (Rotor Quality Factor) measurement provides an overall numerical index of rotor quality, providing a synthetic parameter for component evaluation.
The test can be carried out immediately after die casting, before the rotor shaft is assembled, to identify any macroscopic defects. A subsequent inspection, carried out after the shaft has been assembled and turned, allows the detection of even the most subtle anomalies within the bars.
Permanent magnet rotors
For permanent magnet brushless motor rotors, manual benches and automated stations are available for Back EMF testing.
During the test, the rotor is placed between two centres and rotated inside a sample stator integrated into the test station. By analysing the voltage signals detected at the terminals of the stator windings, it is possible to evaluate the quality of the rotor, the correct positioning and magnetisation of the magnets, identify manufacturing defects and ensure compliance with specifications for optimum motor operation.
When it is necessary to measure the intensity and homogeneity of the magnetic field generated by permanent magnets, possibly also integrating the dimensional analysis of the component, dynamic rotor measurement stations are available. These use magnetic field sensors (such as Hall sensors) integrated into flexible optical measuring devices.
Wound rotors
For wound rotors intended for externally excited synchronous or DC motors, it is generally necessary to perform insulation tests on the windings.
The Partial Discharge Insulation Test (PDIV) technique proposed by the E.D.C., in combination with traditional insulation test methods such as Dielectric Strength (Hi-Pot), Surge, Insulation Resistance, ensures the ability to detect even latent insulation defects that could compromise the quality and reliability of the component in the long term.
It is therefore possible to use similar products and applications for the testing of wound rotors as for the testing of stators, adapting the test methods to the specific needs of the rotor.
Squirrel cage rotors
The following models are available for rotors with diameters between 20 and 400mm and stack heights between 30 and 700mm:
- 7150W basic model suitable for testing medium sized rotors (up to 90mm diameter and 110mm stack height)
- 7150WH model suitable for testing medium sized rotors (up to 400mm diameter and 700mm stack height)
- 7150WA model suitable for automatic lines. Only the acquisition system and in-line probe are supplied.
Special versions can be developed to customer specification for rotors of other sizes.
Permanent magnet rotors
Wound rotors
BROCHURES AND MANUALS
Brochure | |
---|---|
English |
ELECTRIC MOTORS: (1.13MB)
|
Japanese |
ELECTRIC MOTORS: (831.63kB)
|
Korean |
ELECTRIC MOTORS: (2.72MB)
|
Simplified Chinese |
ELECTRIC MOTORS: (5.01MB)
|