Measurement and inspection of membranes
When manufacturing key components of Fuel Cells and Electrolyzers, it is critically important that the main dimensional characteristics are accurate, as well as assuring there are no defects present that could compromise their correct functioning or efficiency.
The production process of components such as membranes, CCM (Catalyst Coated Membrane), MEA (Membrane Electrode Assembly), GDL (Gas Diffusion Layer), flow plates and BPP (Bi-Polar Plates) can generate scratches, tears, ripples, inclusions, contaminants, etc., which, depending on their size, could be particularly harmful.
For the analysis during the product development phase, as well as for sampling in the production line, Marposs offers a semi-automatic station dedicated to quality control on large flat components. This system is designed to carry out precise dimensional checks and provide a complete inspection aimed at detecting different types of defects.
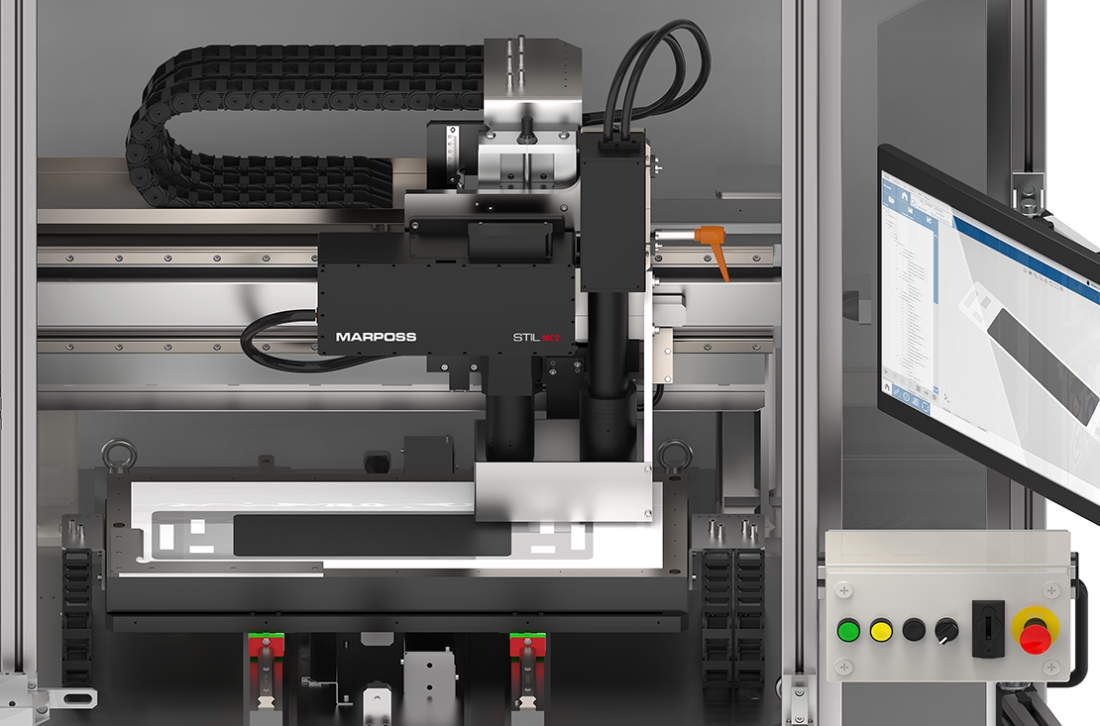
The station employs a combination of different probes based on Marposs-STIL proprietary chromatic confocal technology, which are mounted on machine-controlled axes to automatically perform measurement or retooling strokes.
The MC2 linear confocal camera guarantees the acquisition of very high resolution images with perfect focus on a depth of field up to 2.6 mm, normally unimaginable for high resolution cameras with conventional optics. A very high sampling frequency allows the surface to be scanned in a short time, detecting different types of defects.
The use of MPLS line confocal sensor in combination with the machine axes allows an evaluation of x-y-z dimensions of the component as a whole, as well as of the potential defects that have been identified. Finally, the complete dimensional characterization of these defects makes it possible to evaluate which ones may actually be dangerous for the functioning of the component, enabling the adoption of appropriate corrective actions.
Depending on the type of component and the required controls, it is also possible to integrate different configurations of probes based on different technologies, such as laser profilometers, confocal or interferometric point sensors, linear or matrix cameras.
For example, the use of a point confocal sensor can be used for the control of flow plates and BPPs in order to perform an accurate scanning measurement of the depth and width of the feed channels.
- Flexible solution for measurement and inspection of different flat components
- Part reference equipped with vacuum system for precise and fast positioning, without risk of damage to the component
- Non-contact measurement and inspection technologies
- Complete inspection of the component for a total characterization of any defects that may be present
- Customization of the defect recognition algorithms, also with A.I. methodologies, according to the type of component to be checked
- Control cycle programming with execution of the dimensional measurement only in the areas where the defects are present
Gauge overall dimensions | Width 2,0 m x Depth 1,5 m x Height 2,2 m |
Maximum measured part (x-y) | 600 mm x 200 mm |
Maximum measurable variation in z | 2,6 mm (with MPLS DeepView) |
Maximum retooling stroke in z | 50 mm (to measure parts of different height) |
Scanning speed | Up to 200 mm/sec Depending on the requested performance |
Further technical data (measurement resolution in X, Y and z, accuracy, repeatability, cycle time, …) will depend on the Xed versions for MC2 and MPLS sensors.