Leak Test- Helium
HELIUM TEST BENCH FOR INJECTORS, VALVES AND FUEL RAILS
Our benches are able to carry out tests whose reliability guarantees compliance with the rigorous quality standards dictated by the automotive market.
HeTECH/Marposs has developed specific know-how for testing engine components, such as injectors, CNG valves, H2 multi-valves, CNG pressure regulators, GDI pumps, fuel rail.
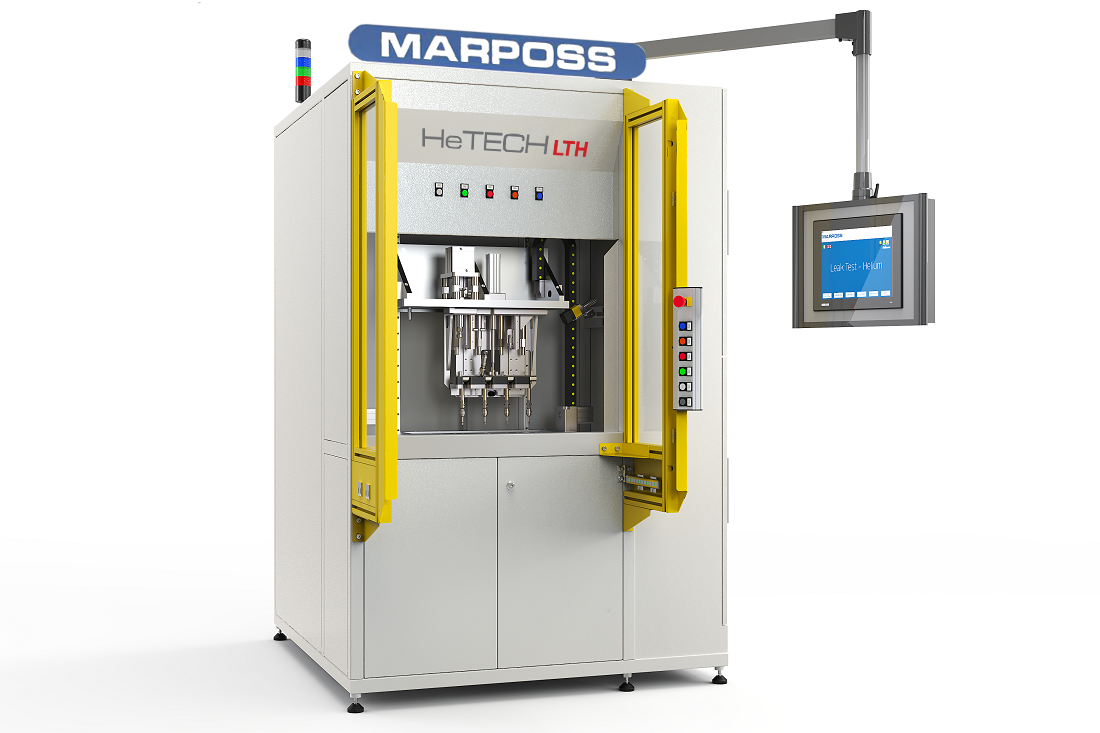
Using helium, not only fine and gross leaks in the component are detected but also the absence of occlusions is verified. If required, it is also possible to carry out the mechanical resistance test of the part being tested.
The layouts of our machines meet any need: the range available starts from compact solutions up to including fully automated assembly lines.
Test pressures, rejection thresholds and productivity that our machines can reach may vary according to the technical specifications of the component and the production needs of the User.
- Dedicated pumping system for the analysis - Total flow
- Pumping system placed on a cart for easy maintenance
- Dedicated Electric and Pneumatic cabinet
- Ventilation and Sound proofing of the pumping system
- Removable & Exchangeable toolings
- Totally customizable HMI interface
- Full traceability of the tested component
- Ready for MES communication