Marposs solutions for LIB electrodes Inline Measurement & Inspection on R2R process
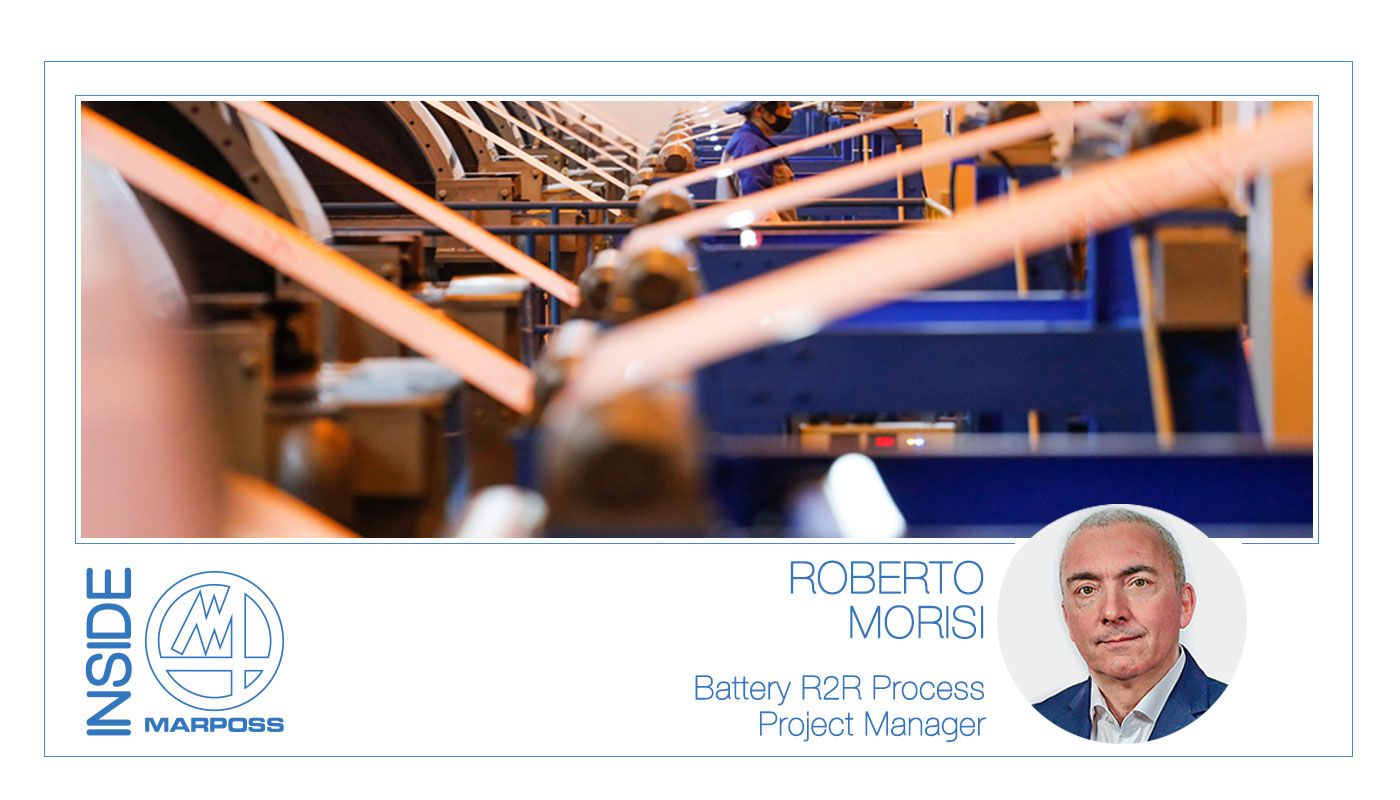
Battery an invention from the past...
The battery. An invention from over 200 years ago that is now more relevant than ever.
The first modern battery, as we know it, was invented by Italian physicist Alessandro Volta back in the 1800s. Batteries have always played a key role in capturing and storing energy, particularly now on Lithium-Ion Batteries (LIB).
Today, Li-Ion technologies are benefiting from massive investment in research and large-scale production for electronic consumer goods and electric vehicles (EV mobility).
... A key Technology for the future
The need for urgent and more intensive action against climate change is widely recognized globally. LIB can therefore contribute to sustainable development and climate change mitigation over the next decade. Batteries have enormous potential as a key technology to achieve the Paris Agreement on reducing greenhouse gas emissions.
Cheaper technology could help accelerate the transition to renewable energy sources. In this respect, the growing popularity of electric vehicles is fuelling a large demand for LIB in the coming years. The volume of the global market for the high-quality production equipment needed to create numerous Giga Factories will grow by more than 30% per year until 2030.
In the high-cost production chain of LIBs, the processing of electrode foils (cathode and anode) using 'Roll to Roll' (R2R) processes is one of the most important steps in the production chain. Here, increasing the speed of production lines and minimizing waste could help to reduce costs and thus achieve the above goals.
Marposs: Inline measurement, inspection and quality control for LIB production process
The challenges associated with electrode production are stage-specific. Let's see which are the main operations in electrode manufacturing and where Marposs fits in with its Inline measurement, inspection and quality control systems.
Measurement of Electrode Coating and Drying: Chromatic Confocal Probes
For electrode formation, the components (metal foil and slurry) are mixed with a solvent and coated roll-to-roll on the metal substrate as a liquid film. The metal foil is as thin as possible, with only 20 μm (aluminum) for the cathode and less than 10 μm (copper) for the anode. The amount of coating on the surface of the electrode film is determined by the requirements of the future LIB cell.
High energy applications require much thicker films for higher specific capacitance. This usually results in dry electrode thicknesses in the range of 30-200 μm. In LIB electrode production lines, the drying step directly follows the coating step.
At those stages of the process, it is essential to control the homogeneity (no blank spaces) and uniformity (continuous thickness) of the coated electrode. Even if defects or contamination on the surface are not present and the edge geometry of the coating is clean. Chromatic Confocal technology enables in-line inspection of coating thickness and edge geometry to be carried out with high accuracy and high frequency sampling.
Marposs, with its affiliate STIL, is able to offer a wide range of high performance optical equipment. With about 30 years of experience STIL is the inventor of chromatic confocal imaging, a leading technology for non-contact sensors. STIL has designed two families of sensors based on this innovative technology: point sensors (from 0.1 mm up to 100 mm measuring range) and line sensors (from 1.35 mm up to 4 mm line length with different measuring ranges).
Measurement and Inspection of Electrode Calendering: Confocal technology
The cathode and anode electrodes leave the drying stage and to increase the energy density, the films are calendered. During the calendering, the electrode coil is passed through a roll press to compress the active material, decreasing the film thickness and the porosity. The main goal is to reduce the electrode volume to increase the volumetric density and to flatten its surface.
Compressing too much the electrode could result in reducing its porosity to a level which electrolyte cannot penetrate in its structure. The quality control requirements here are quite similar to those of the previous coating step process. The deviations in the thickness of the final electrode have to be carefully controlled. Also defects as drop off coating, fatal damages and pinholes have to be inspected as consequence of non-homogeneity formed during the coating step.
Stil/Marposs confocal technology once again represents the optimal solution for geometrical measurement and inspection during this critical process step.
Slitting of electrodes: Laser Micrometer Measuring system
Slitting is a separation process in which a large electrode coil (mother roll) is split into several smaller electrode coils (daughter rolls).
The total length of the raw electrodes processed from roll to roll can be up to 2000 m with a width greater than 1000 mm. The requirements for this process are different because due to the very abrasive cathode materials, the electrodes are cut by ceramic blades.
Geometric measurement data is an important step of the process, to identify the wrong position of the blade or of the electrode to be slitted. The cut quality of the electrode edges and the cleanliness of the coils are considered as the main quality criteria. The cutting width of the daughter rolls can vary depending on the cell design and lies between 60 mm and 300 mm in many applications.
Crucial is the monitoring of the width process of this step to reduce excessive scrap rates of electrode production by means of quality measurement and in-line control such as non-contact technology.
In order to perform in-line width measurement on delicate material that cannot be touched and measured with traditional contact solution, Marposs/AEROEL proposed its own Laser Scanner Micrometers.
Thanks to their non-contact measurement capability, AEROEL Laser Scanners can be applied quickly, accurately and efficiently to R2R industrial processes. Also, for the production of LIB electrodes, laser optical technology ensures consistent, objective and accurate results directly at the factory. Innovative technical solutions, guaranteed by patents, have allowed us to realize quality control systems insensitive to temperature variations, vibrations, foil movement, dust and other environmental conditions that would normally affect measurement results in the production environment.
Inspection on Separation (Notching) of the Electrodes: Machine Vision Solution
Separation or notching is required for the production of the pouch cell and describes the separation of the anode, cathode, and separator sheets from the roll material (daughter rolls). The notching process is usually performed with a shear cut (punching tool) or laser cut in a continuous process.
The most important quality parameters to be inspected during this process step are: burr quality, cutting edge geometry, foreign metal particles, and deformation of the electrode microstructure.
Metal shavings on a micrometer scale could also damage the sensitive separator and cause short circuits in the finished cell. Thus, defects are so dangerous if they come out of the coating (effects of currents and electric fields or short circuits). Therefore, it is important to check the deviations of the metal foil (aluminum or copper) from the nominal center position of the electrode.
Marposs can solve the defects control thanks to a Patent Pending in-line Machine Vision solution. The system can statistically check and follow a negative trend in the quality of the electrode profile identifying the existence of burrs, folds, and delamination.
The Vision Inspection System has a High-Resolution Linear Camera that frames the edge of the electrode and acquires a series of digital images, which are analysed to check for the possible presence of metal burrs. The system also includes a Matrix Camera, which detects a change in distance between the edge of the electrode and the Linear Camera. The processing device (controller) is configured to vary the focus of the Linear Camera according to the change in distance between the edge of the electrode and the optical system.
At this point, after these R2R process steps, the LIB electrodes are ready for the cell assembly process, which includes stacking, packaging, filling, and sealing the electrolyte, followed by the first electrical charge.
In the area of LIB process improvement, there are mainly innovations in electrode production and cell finalisation that are helping to increase production.
Marposs can also guarantee for LIB cell assembly quality measurement and inspection solutions for the production flow, by means of different parameters monitoring and technology.
Marposs Group, thanks to a wide range of technologies and solutions, aims to play a leading role in quality and process control in the world of electro-mobility.
Discover more about Marposs Inline Measurement & Inspection solutions for R2R process