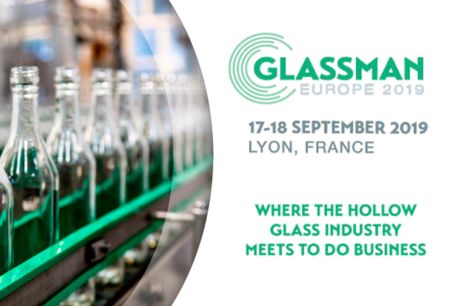
Our Glass Containers Industry Manager, Eleonora Bordini, talks about VisiQuick-mini, the new compact, flexible, semi-automatic bench introduced by Marposs for glass containers measurement on a sample basis.
Ms. Bordini will be presenting at the Glassman Europe conference in Lyon, France, on September 18, a paper titled ‘How to use QC Lab technology in a production environment’. A VisiQuick-mini unit will be also on display at Marposs booth.
To know more, read the whole article published in the July - August 2019 issue of Glass International:
Glass container manufacturers can keep production under control, at the cold-end, in various ways:
- Periodically bring a batch of containers taken from the line in the quality control laboratory for an accurate measurement with a sampling gauging machine;
- Install, near each manufacturing line, after the annealing lehr, a gauging table with go-no go gauges for periodic manual control of a production batch. The second approach, allows the timely detection of production problems, without the need to bring containers to the laboratory and wait for gauging machine availability.
A control carried out with hard gauges has drawbacks:
- Results depend on the operator’s skill.
- The necessity to buy, manage and periodically calibrate a large number of go-no go, with related costs.
- Controls by attributes can highlight a problem (for example a too small inside diameter), but not provide any quantitative indication.
- Does not allow data collection, and therefore statistical analysis and the possibility to promptly detect process trends and deviations.
Controls carried out with go- no go gauges typically include: Height, verticality, inside diameter, a few parameters on the finish (for example thread diameter and ring diameter), and body diameter.
Usually a scale is also present on the gauging table to measure the containers’ weight. The control of a production batch, including one container per mould present in the forming machine, takes between 10 to 30 minutes, according to the number of containers and number of gauges involved.
Marposs has designed and is ready to deliver a flexible and compact (1.000mm x 700mm x 1.000mm) measuring system, based on optical technology, to replace all hard gauges for external dimensions measurement.
VisiQuick-mini can measure, without any job change, and with laboratory quality level, glass containers that, regardless of their colour and shape, have the following overall dimensions:
- height ≤ 410 mm.
- external body diameter (or diagonal for non-round containers) = 30 - 120mm.
The container to be measured is manually placed on a rotating plate, that can also travel along a vertical axis, to bring the portion to be measured in front of a high resolution camera with compact telecentric lens and backlight illuminator. An optional industrial scale can be integrated in the mechanics of the plate, to measure the container’s weight.
Measurable characteristics include most of the measurements already available on the external dimensions measuring station of the VisiQuick machine, i.e height, verticality, bent neck, mouth parallelism, body parameters (e.g. diameter, long/short sides and diagonals on non-round containers, height of a given diameter, etc…), finished parameters on any finish type (e.g. diameters, heights, angles, radiuses, etc…).
After selecting the recipe of the article to be measured and entering the mould numbers sequence, the operator manually loads the first container on the rotating plate and starts the measuring cycle.
The plates travel, in a vertical direction, to bring the portions of the container to be measured in the camera range. In each position, the back-illuminated container rotates and its images are focused on the camera’s sensor and measurements are acquired.
When the measuring cycle is finished, a light warning device informs the operator that the measured container can be removed.
The same measuring cycle is repeated for the second and next containers of the batch. Cycle time depends on the container height, the number of characteristics to be measured and their position.
Average cycle time is in the range 30 - 60 sec.
VisiQuick-mini allows the collection of data that can be integrated with production monitoring systems, such as Vertech SIL. VisiQuick-mini can of course be also installed in the laboratory. This option is convenient for customers with a limited budget or plants located in countries with low labour costs.
Read more about VisiQuick-mini