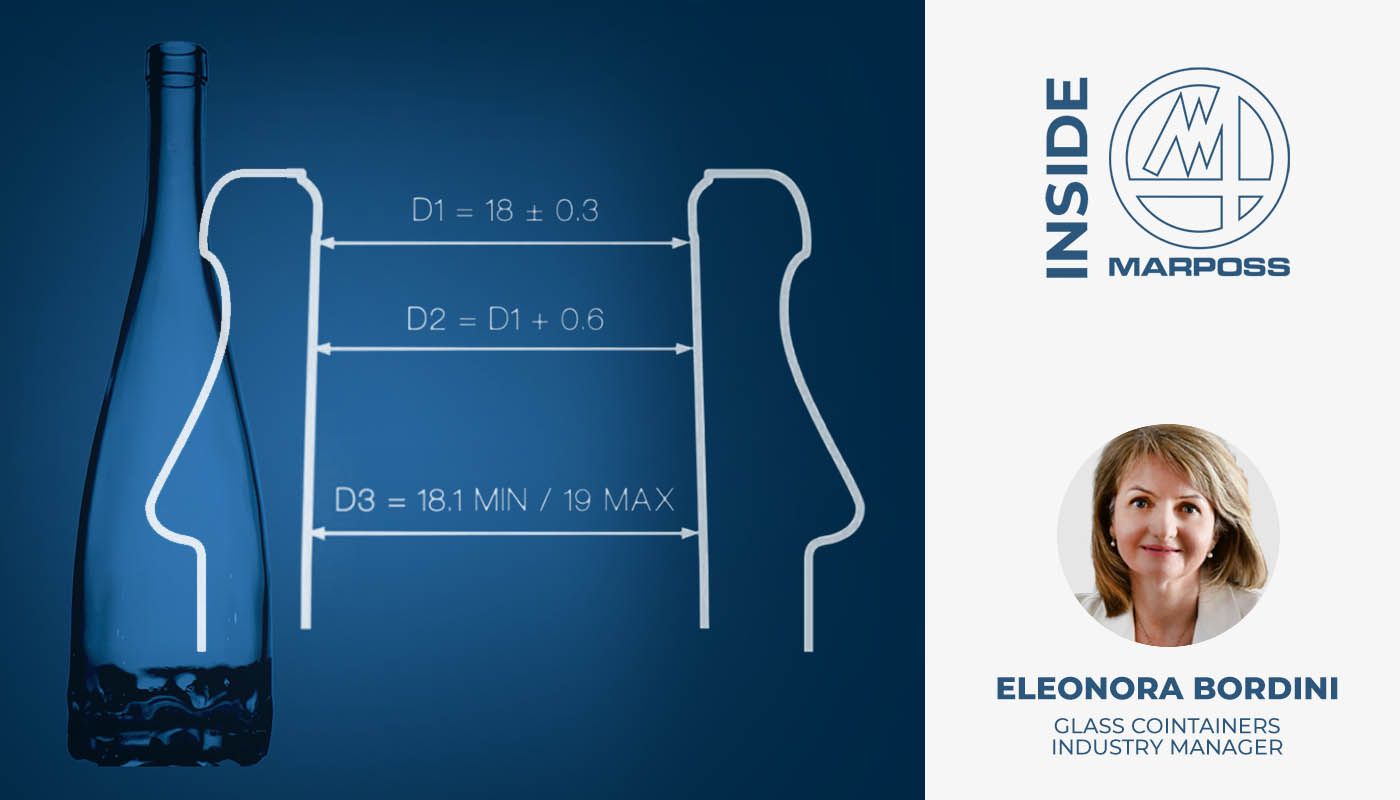
ID SCAN, a comprehensive solution for measuring inner diameter and profile of glass bottles, in production environment, at the cold-end or at the hot-end
Glass is, for several reasons, the consumer preferred packaging material for different food and beverage products and it will become more and more popular in the future, thanks to single-use plastic ban, introduced in EU and other countries, and even more thanks to a growing environmental consciousness of the consumers.
Glass is inert, odorless and flavorless, nothing passes from the glass into the product and nothing penetrates from outside through the glass into the product. It protects the content’s taste and quality better than any other packaging material. Glass is a sustainable material, 100% and endlessly recyclable. Glass is a premium material, enhancing the content. In the popular imagination, glass packaging is associated to a higher quality product.
When we think of wines, spirits, high quality olive oils and vinegars we think of glass. These products in glass bottles are engrained in our history and tradition. Glass preserves the content but also allows it to age, sometimes for many years.
Of course, in order to protect the content, glass bottles must be correctly sealed to prevent oxidation. A huge variety of external or internal closures and stoppers are available to seal glass bottles.
Internal stoppers for wines are made of natural cork or synthetic material. In order to hold it in place, the internal shape of the bottle neck, in the cap area, must be barrel shaped. In fact, the stopper, subject to internal pressure, would not stay in place in case of a substantially cylindrical internal shape.
Olive oil bottles generally uses screw caps associated with drip catcher, inserted in the bottle bore. The bottle bore, in the area in contact with the drip catcher, must have tight dimensional tolerances. A too big inner diameter would not retain the drip catcher, while a too small one would not allow it to be inserted. Spirits bottles use pouring stoppers with safety closures that don’t allow to fill it with other liquids, to avoid adulterations. Also in this case, tight tolerances on the container’s bore have to be guaranteed.
More in general, any glass bottle, irrespective its content, has to be filled and must allow the insertion of the filling tube, so a minimum inner diameter is required to the bottle neck.
Consequently, glass containers manufacturers must keep under control inner diameter and profile in any phase of the manufacturing process. For this purpose, it is necessary to use reliable measuring instruments providing all the information necessary to prevent the production of scrap containers that would lead to customers’ claims.
In production environment, bore diameter is usually checked with go-no go or manual gauges. When available, semi-automatic or automatic systems are generally present only in the quality control laboratory. Anyway, it’s too time consuming to bring containers to the laboratory only for measuring bore diameter and profile. In some situation, for example at production changeovers, it is necessary to get immediate information at the hot-end to promptly adjust production parameters.
The use of go-no go or manual gauges has several drawbacks. It does not allow to obtain comprehensive information about the characteristics to be measured. Results relies on the operator’s skill. Data are not collected, so process trends cannot be detected and information available is not enough to set-up and control the process.
Marposs has developed ID SCAN, a new semi-automatic system, with manual loading/unloading, dedicated to bore diameter and profile measurement. It is available in two versions: ID SCAN CE for use at the cold-end and ID SCAN HE for the hot-end.
To achieve accurate measurements ID SCAN uses a single contact tactile sensor. It can measure automatically and without any mechanical retooling, bore diameters in the range 13-50mm, at one or more depths, and it can also perform vertical scans, to determine the internal shape, up to a depth of 70mm from the top.
The result of inner diameter measurement is maximum, minimum and average values at the programmed depth and a graphic showing the bore real shape is also available.
The result of the internal profile measurement is a graphic showing the diameter variation in the scanned area.
Measurements results, related to the mould, can be sent to a Manufacturing Execution Software (MES) and can be also saved locally.
Recipes related to the articles to be measured can be automatically generated by the MES and sent to ID SCAN. In this case, no programming is required by the operator. As an alternative, recipes can be also programmed locally.
ID SCAN contributes to enlarging the range of Marposs products for glass containers measurement in production environment. It joins the well-established VisiQuick and VisiQuick-mini, confirming Marposs commitment to support, more and more, glassmakers with innovative high performing measurement, inspection and testing solutions.
More information about Marposs solutions for the glass packaging industry are available on Marposs website