Bris d'outil sur centres d'usinage
L'absence de détection de bris d'outil au cours d'un processus d'usinage risque d'avoir des conséquences dévastatrices sur la production.
Tout d'abord, chaque pièce que fraisera l'outil endommagé à partir du moment de sa cassure sera mise au rebut. Cette situation s'aggrave en cas de production sans personnel, où de nombreuses heures passeront avant qu'un opérateur identifie le problème.
Ensuite, dans les processus comme l'alésage, les outils utilisés sur une pièce après leur bris sont probablement endommagés car ils risquent d'enlever plus de matière qu'attendu, et prévu par leurs caractéristiques.
Pour éviter ce type de perte et de coûts, il est impératif d'équiper la machine d'efficaces systèmes de contrôle d'intégrité d'outil, qui identifient le moindre bris juste après un processus d'usinage.
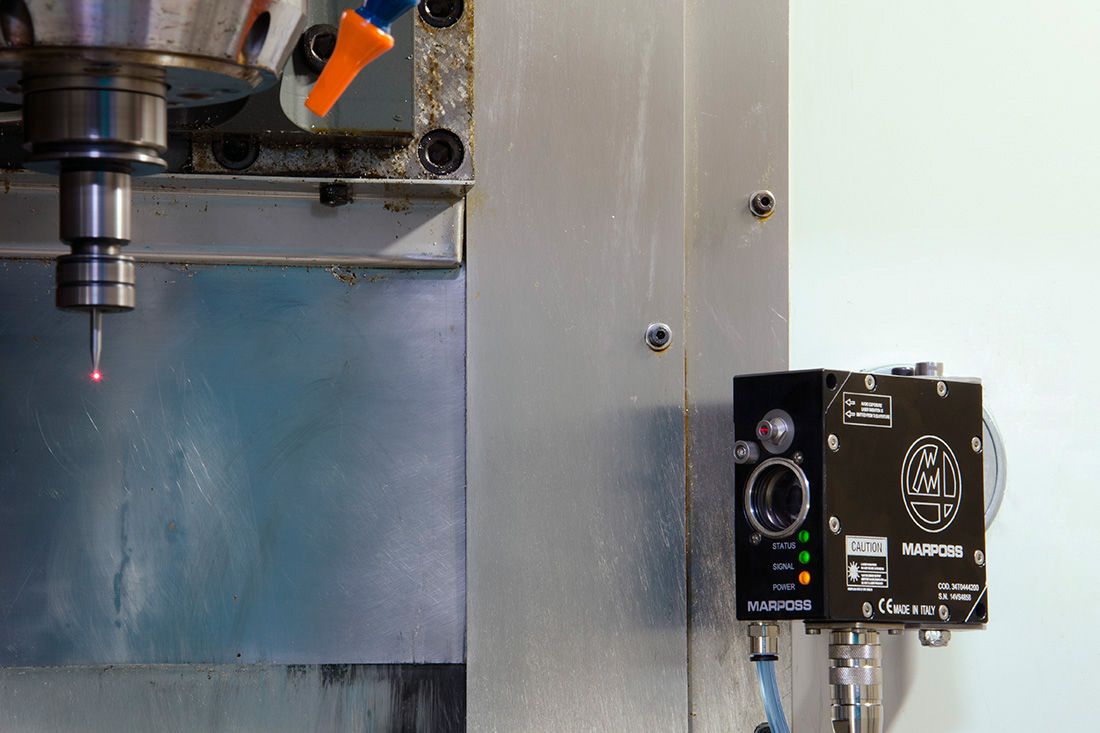
Marposs propose différentes solutions pour la détection de bris d'outil et le contrôle d'intégrité. De tels systèmes sont faciles à installer et configurer, et opèrent avec des cycles logiciels extrêmement rapides, en garantissant ainsi à la fois qualité de travail et optimisation du temps de cycle.
Les produits Marposs pour bris d'outil prennent pour référence initiale les dimensions dans une table outils et nécessitent la définition de la tolérance maximale de bris admissible par l'opérateur (valeur minimum 0.1 mm). Après l'usinage, le contrôle est effectué : en cas de détection d'un bris supérieur à la tolérance, un signal d'alarme est généré pour que l'outil endommagé soit remplacé, en évitant des problèmes de production.
- Meilleure qualité de production
- Meilleure productivité de la machine
- Moins de rebuts, notamment lors des opérations en l'absence de personnel
- Contrôle automatique de l'intégrité de l'outil
- Contrôle rapide
- Activités de l'opérateur facilitées
Il existe différents systèmes de détection de bris d'outil :
- Systèmes de réglage d'outil par contact, parfaits pour les plus gros outils (diamètre minimum 1 mm) Disponibles avec transmission via câble et sans fil (radio et optique)
- TBD, ou Tool Breakage Detector, est un détecteur de bris d'outil destiné au contrôle d'intégrité axial, essentiellement pour outils monoblocs (ex. mèches et outils de taraudage). Il peut identifier de très petits outils, de l'ordre de 0.15 mm, en moins d'une seconde
- Mida Laser, système sans contact qui, en dehors du contrôle d'intégrité, garantit la capacité de réaliser différentes mesures et le balayage du tranchant;
- Vision Tool Setting, idéal pour les micro-outils et applications nécessitant des performances métrologiques exceptionnelles (précision de mesure inférieure à 2 microns).