Leak Test Air
PEM FUEL CELL BIPOLAR PLATE LEAK TESTING BY PRESSURE DECAY MEASUREMENT
Leak testing is a key test operation in the Bipolar Plates production process, thus it verifies the tightness of Hydrogen, Air and Coolant circuits of the flow plate, simulating real operating condition. The design and construction of the fixture and of the sealing are foundamental, which know-how belongs totally to Marposs Group. The perfect circuits configuration and sealing of the Bipolar Plates are the most important features to guarantee efficiency and long lasting of the stack and the complete fuel cell system.
The leak test guarantees the Bipolar Plates correct production (by stamping or hydroforming and welding, gluing or brazing) and assess the safety and the efficiency of the stack/fuel cell system once operating. Accordingly, the tightness of the bipolar plate is of paramount importance to ensure efficiency, long term reliability, quality and safety standards of the fuel cell electric vehicle.
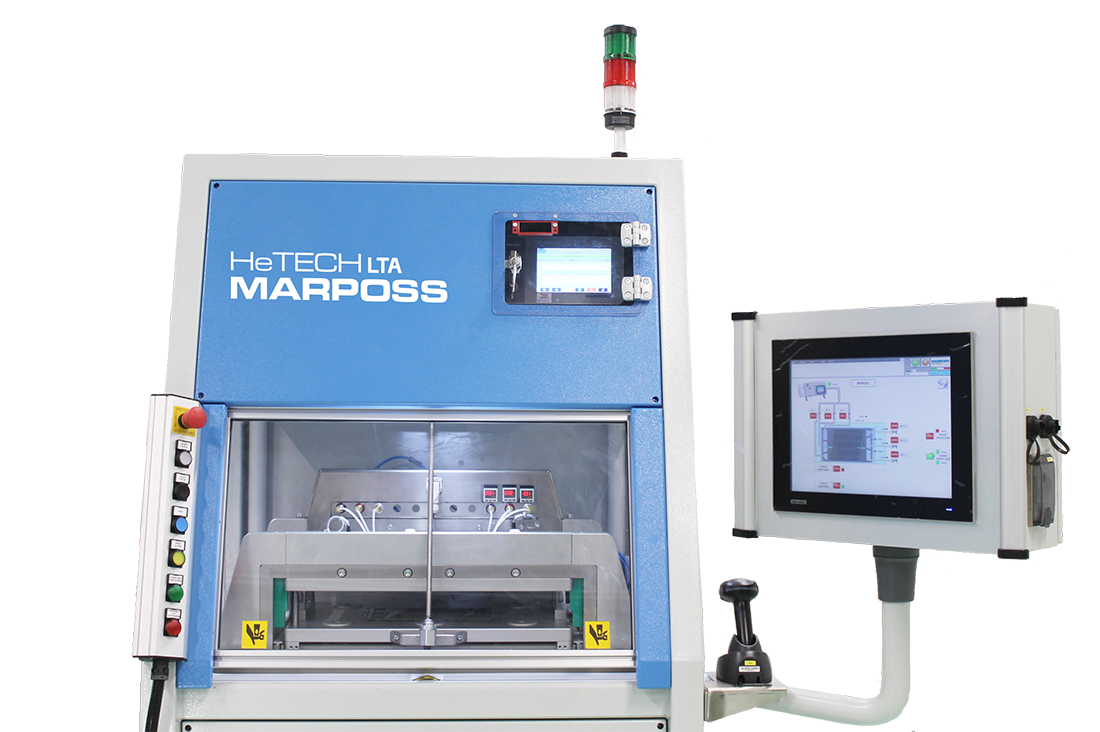
One test module machine for Bipolar Plates with manual loading/unloading. The test fixture consists of two removable plates, upper and lower, containing sealings which comply with the Bipolar Plate pattern and make tightness against each of the three circuits (Hydrogen, Air and Coolant). The Bipolar Plate is placed on the lower plate. After the manual closing of the fixture, the Bipolar Plate lays between the upper and the lower plates of the fixture for the testing operation.
Principle of measurement: pressure decay test with air, by way of Tecna T3LD measuring device.
Machine can be upgraded for automatic loading/unloading by robot, pick & place or any automatic system.
The testing station provides a single station, assembled on a welded painted steel frame with cover panels and vertical automatic door. A pressing system for the fixture compression during the test is placed in vertical position while the horizontal opening and closing of the testing fixture is guaranteed by a sliding guide system.
The cabinet containing the electric switchboard and the pneumatic distribution system is placed behind the testing area.
HMI is made by a touch-screen color monitor positioned into a box in turn fixed to an arm on the side of the testing station; push-buttons and light signals for the operator are positioned on the left side of the station.
The access to the testing area is protected by the automatic door and only electrical and air supply are needed to run the machine.
One measuring device Tecna T3LD is installed in the testing station and it measures the pressure decay of the Bipolar Plate’s circuits using the pressure differential method: a pressure difference between the product being tested and a reference sample (with a reference volume) is detected.
The fixture, once manually closed, is automatically actuated and allows the coupling between the testing station and each circuit to be tested.
The bench incorporates an industrial PC which performs HMI functions while supervision of the process is made by a PLC. The software is configurable so that it is possible to:
- Set machine parameters
- Create different recipes, according to required test parameters
- Manage the automatic cycle as well as the manual cycle
- Set counters and production data
- Manage levels of access
- Development of customized sealings and couplers to make perfect tightness on such a peculiar component.
- Development of new systems to avoid component deformation.
- Easy access to process circuit by way of front, side and rear doors.
- Configurable HMI touch screen interface.
- Push button panel and light signals for easiness of the operator.
- Experience gained in a significantly increasing new market segment to support other customers in the development of similar projects
- Test Pressure: 1,0 bar (rel)
- Leak threshold: 0,25 ÷ 0,30 sccm
- Measuring time: 5 s
- Manual loading/unloading (possibility to implement an automatic loading/unloading)