In-line leak test: Advanced industrial solution for the white goods industry
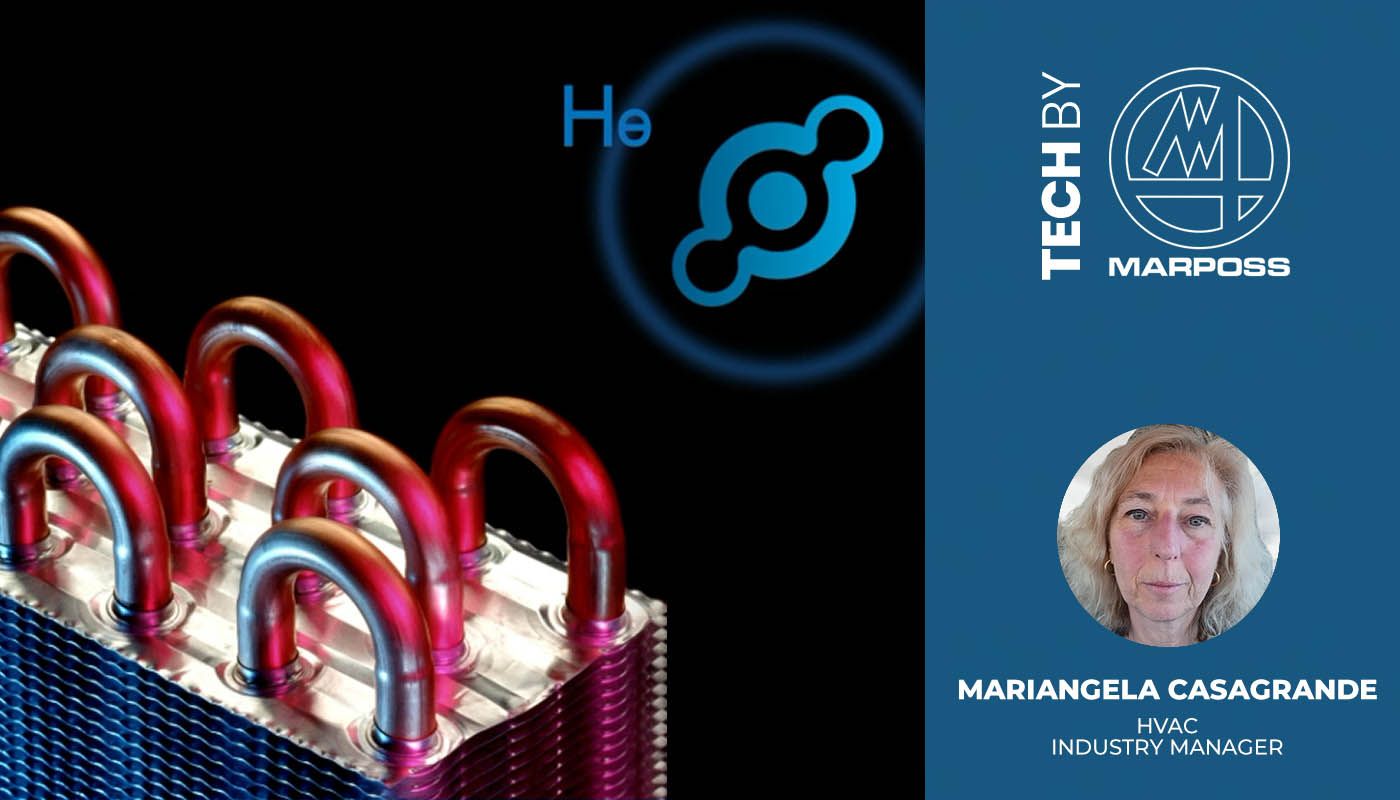
Leak test of the dryer heat pump assembly
The automatic leak test lines have been installed on the production lines of the dryer heat pump assembly.
In the context of the white goods industry, the dryer heat pump leak test application is a high-tech end-of-line test that allows the manufacturer to guarantee a very high quality of its final product, without giving up the high productivity that it must maintain to satisfy the market demand with real production sites.
Hard vacuum helium leak test technology
In this solution, the hard vacuum helium leak detection system applied to the entire finished assembly provides the most reliable method for detecting overall leakage on the circuits.
In the test method, the tracer gas is 100% helium and the analysis system is mass spectrometer measurement in a vacuum chamber; this method is the most efficient among the different leak test systems, aiming at the detection of the smallest amount of leakage, values.
In-line leak test machines are capable of testing heat pump assemblies with leakage thresholds in the range of 10-5 mbar*l/s, under an applied test pressure of 40 bar. This solution gives a productivity of 150 pcs/h, in fully automatic production.
Full automation matches with high tolerance mechanical assembly
A very flexible design of the coupler allows for automatic connection of the inlet pipe, despite the very uncertain positioning in the assembly. The coupler has a high compensation capacity, even when covering a large distance up and down to reach the connection point with a vertical pneumatic movement. A most likely applicable manual test was performed fully automatically, with enormous advantages for production.
Our contribution towards a green planet
Leak testing is a fundamental operation in all heat exchange processes using refrigerant gases, in order to ensure the long-term tightness of the components where the refrigerant gas is contained, as well as to guarantee the performance in terms of heat exchange efficiency.
The need for highly accurate leak testing of HVAC products is driven by two factors:
- The proactivity of governments in controlling the climate and, as a result, stricter regulations.
- The growing demand for energy-efficient heat exchange systems.
With regard to climate control, increasing attention is being paid to the potential contributions of refrigerant compounds to global warming. For this reason, the most reliable and accurate leakage control solution must be used and all parts and connecting circuits must be assured to meet total leakage below that allowed by law (specific thresholds for any chemical compound). To achieve the efficiency of the thermal assembly in its final installation, leakage detection gives an important confirmation that the efficiency of the heat exchange will not decrease within a reasonable warranty period until the use and consumption of the parts becomes relevant. Marposs solutions are strongly focused on developing the best leak test performance for more efficient products.
Benefits of quality inspection
A preliminary rough leakage test is carried out on the entire dryer heat pump using the air pressure decay technique, so that in the event of a large defect on the part, the following benefits are achieved:
- Reducing helium consumption
- Avoiding helium contamination in the analysis system.
- Stop the fine leakage test on NG parts and thus save time.
- Quality data management for production process adjustment
A manual sniffing system is always included in HLT vacuum machines, to allow maintenance, troubleshooting and identification of the leak position again for corrective actions in the production process.
The complete traceability of the tests is developed for the guarantee from the manufacturer to the final customer.
Cost reduction even with high quality production controls
A high efficiency (85-95%) helium recovery system is connected to the leak test machines, recovering the helium used for each test cycle and processing it so that it is ready to be re-fed to the leak test machines in a closed system.
The purity of the helium is analyzed and corrected if necessary by filling and final compression of the storage helium to the required test pressure. The result of the recovery provides set points for leak testing at the HLT machines, so that data outside the acceptable range generates alarms preventing false leak detection. A fully integrated process gives the system greater accuracy and reliability.