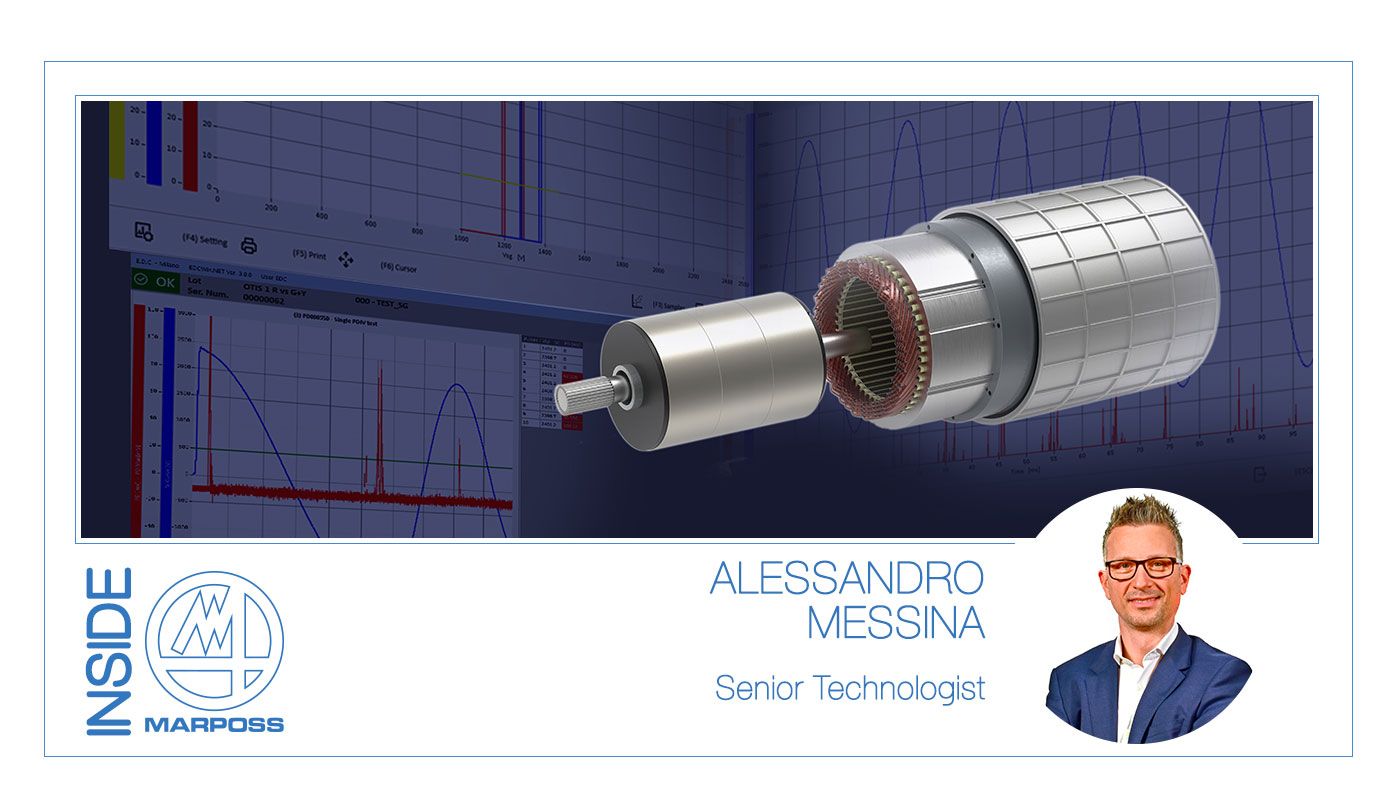
The electric motor is experiencing an unprecedented global growth trend. This fast diffusion on a large scale in the automotive sector, creates high expectations for the components reliability by both manufacturers and end-users, which has implications for quality and process control requirements along the production chain.
The ever-rising attention for the high reliability of electric motors, is prompting and resulting in a production shift towards higher quality standards.
Facing a new era with new technologies
For almost seventy years, Marposs’ mission has been working side by side with customers to guarantee quality control in production processes. Thanks to the wide range of technologies and products available, and a worldwide presence, Marposs has been the ideal partner for OEMs, first and second tiers, as well as machine tool makers operating in the automotive industry.
Now - in times of great changes, such as the transition to electro-mobility - Marposs aims to stay a strong reference for the automotive market to face the new challenges of the e-mobility era.
Marposs e.d.c: Partial Discharge Measurements
Thanks to the acquisition of e.d.c, in July 2020, Marposs is able to offer customers a wide range of customized testing solutions for the electric motor and its components, for both production and laboratory environments.
The strengths of e.d.c. relies on the high specialization in Partial Discharge Measurements: more than 20 years of experience and over 8000 systems installed worldwide, allowed e.d.c. to develop a technology that, unlike standard tests such as Hi-Pot and Surge, identifies 100% of defects, even the latent ones.
The Partial Discharge Measurements allow to detect all latent defects that could generate failures in e-motors, after short operating times. This is even more true for electric motors powered by Inverter - like electric vehicles - which, due to the inevitable voltage overshooting, causes more stress to the motor windings.
The standard electrical tests are not enough to identify all types of failure. Many defects produce just partial discharges which can be identified only by using the Partial Discharges testing method. This does not replace the standard tests but has to be performed in addition.
A typical fault that occurs, for instance, is when a wire touches the stack of the stator. If the wire has the enamel scratched in the contact point with the stack, even the standard AC Hi-Pot test is able to identify the fault. But, as commonly happens, if the wire is well insulated, the voltage applied during the AC Hi-Pot Test, even if quite high, could be not sufficient to break the remaining insulation material and this fault could be not identified. With the measurement of Partial Discharges carried out at the same time of the AC Dielectric Strength Test the 100% of these defects are always identified and filtered.
The consequence of permanent partial discharges is a gradual but continuous weakening of functional parts of the insulation system, that leads to a complete breakdown and to a failure of the electric motor. That is why there shouldn’t be a partial discharge in the electric motor during operation and that is why e.d.c Partial Discharge testing method is so precious for automotive manufacturers, even for Tier 1 suppliers.
Marposs solutions for motor testing
Motor testing is designed to check the integrity of an electric motor through the use of equipment that identifies potential trends within the motor.
The main objective of motor testing is to reveal latent problems and prevent unnecessary failure evaluating static parameters like insulation, wire damage and electrical current leakage, as well as more dynamic parameters such as Back EMF (ElectroMotive Force), NVH (Noise Vibration Harshness), speed and torque diagrams, three phase short circuit, cogging, torque ripple.
With the e.d.c. products, Marposs offers a complete range of solutions dedicated to the functional testing and the end-of-line testing of any type of electric motor, for in-line and off-line applications or for laboratory analysis and characterization.
Marposs provides customized inline and offline solutions for all electrical tests and detection of insulation problems at all stages of development and production of an e-motor and their components, such as:
- Stator Tester for production lines (wound or hairpin) that includes Partial Discharges measurements,
- Rotor Tester for all kinds of rotors (with permanent magnets, squirrel cage, wound),
- Automatic EoL Motor Tester (with Load/No-Load tests) for production, Dynamometer for motor Load Test & Life Simulation Cycles for laboratory,
- Advanced Windings and Insulation Quality Analysers for laboratory
Quality control of stators
Quality control of stators means checking various electrical characteristics along the entire production chain. In particular, the insulation tests with Partial Discharge measurements carried out in different stages of the process represent a key operation in assessing the quality and reliability of the component.
Functional control of the rotors
The functional control of the rotors depends on the type of electric motor adopted and therefore on the rotor configuration: for squirrel cage rotors the quality control is carried out either manually or with fully automatic testing stations (for in-line integration), whose purpose is to identify defects inside the die-cast bars of the cage such as interruptions in the material, porosities, defects in the connection to the end ring, geometric and shape errors.
In case of permanent magnet rotors manual benches or automatic stations are used to perform Back-EMF tests with FFT analysis.
End-of-line functional test
The end-of-line (EoL) functional test represents the key operation for the quality control of the fully assembled electric motors, it is responsible for the overall functionality of the product at the end of the manufacturing process.
The methods for carrying out the functional check may differ depending on the intended use for the testing station, for analysis activities in the Laboratory during the product development and process set-up phase, or for the 100% quality control at the end of the assembly line.
In production the complete quality control of the electric motor includes the insulation tests, in order to verify that the assembly operations have not compromised the perfect state of insulation, and a series of functional tests in order to evaluate dynamic parameters such as Vibration (NVH test), Dynamic or Passive BEMF with FFT analysis, Friction & Iron Losses, Zero Resolver Position and more.