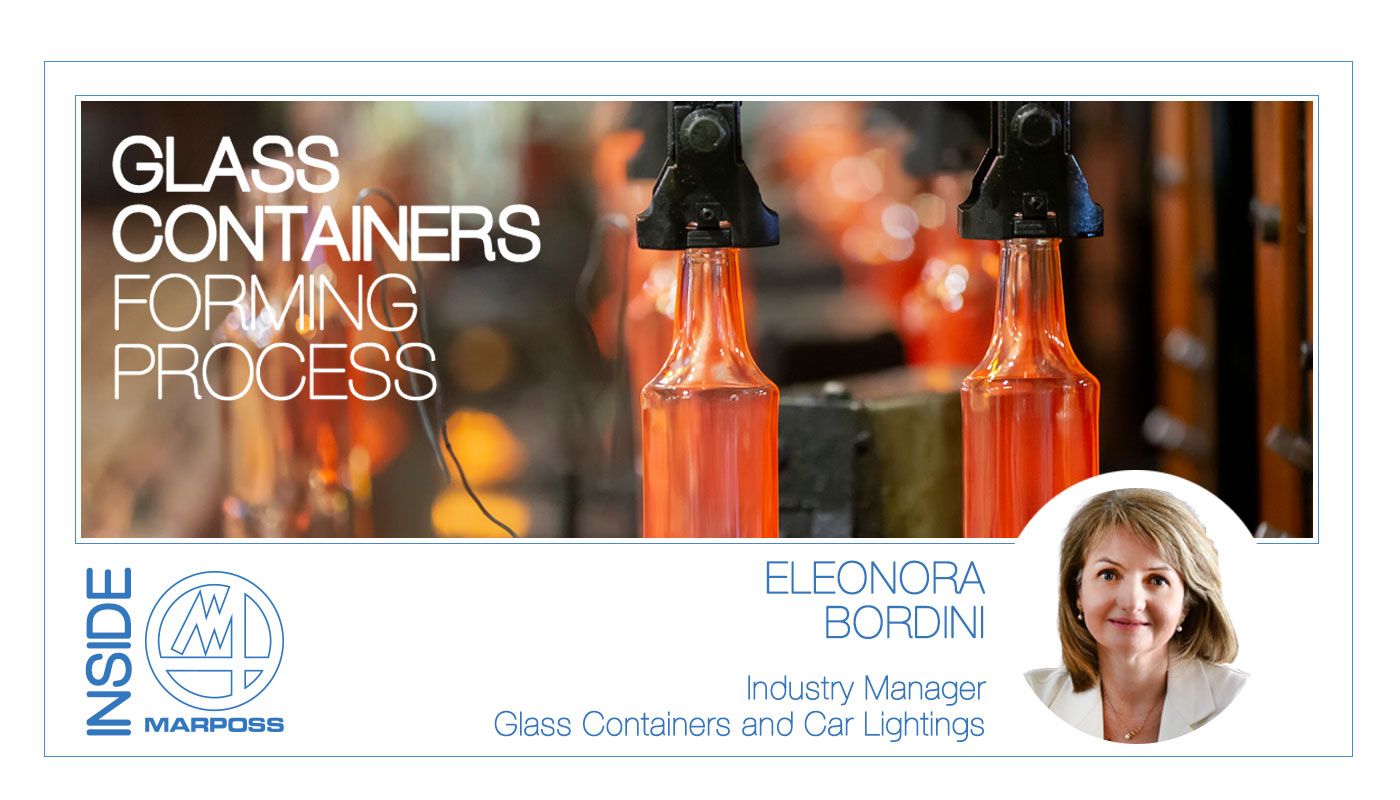
ガラス製造の進化
ガラスは最も古い素材の1つです。ガラスの歴史は紀元前3500年に遡ります。紀元前1500年に、最初の中空ガラス容器がエジプト人によって製造されました。
紀元前 1 世紀に吹き矢が発明されたとき、技術革命が起こりました。20世紀初め、米国でマイケル・オーエンスによって発明された最初のガラスびんの自動生産で真の革命が起こりました。1時間あたり最大2,500個の容器を製造することができ、工業規模でのガラス容器製造が可能になりました。
1925年ブローブロー成形、またはプレスブロー成形技術を使用した最初の工程別マシンで、この技術はさらに改良がされ、今日でも使用されています。すべてのセクションでは複数の容器を個別に生成します。溶けたガラスの塊は、技法に応じて、事前に吹き飛ばされるか、プランジャーでプレスされ、空洞の型に落ち、びんの原形に成形されたゴブ(パリソン)は仕上げ金型に移され、圧縮空気でびん形状が完成します。
現在の成形機には最大20の個別セクションがあり、各セクションで1~4個の容器を同時に製造することができます。これは、各セクションに存在する1~4個の型に、1~4ゴブ (SG = シングルゴブ、DG = デュアルゴブ、TG =トリプルゴブ、GD = クワッドゴブ) が移されます。そして、これは各セクションで並行して行われます。容器の大きさや形状にもよりますが、生産速度は700個/分の速さです。
ガラス容器:特性と長所
ガラス容器は、さまざまな業界のパッケージとして使用されます。
- 食品・飲料
- 香水・化粧品
- 医薬品
ガラスは不活性物質です。ガラスから製品に混入するものはなく、外部からガラスを通過して製品に混入するものもありません。
ガラスは持続可能 (100%リサイクル可能)な素材です。
ガラスはプラスチックやアルミニウムなどの他のパッケージ素材と比較して美しく、製品の価値や品質を高めます。
いずれにしても、ガラスは他の素材に対してはるかに重いです。しかしここ数年で製造工程が改善され、軽量の容器ができるようになりました。ガラス容器は、20年前と比較し最大40%軽量化されています。軽量化は輸送コストを削減するだけでなく、何よりも原材料とエネルギーを節約するために必要なことです。
溶解炉も大幅な技術改良を行い、エネルギー消費量とCO2排出量を削減しています。
ガラス容器の形状はますます複雑化しています。ユニークな形状は、商品価値(プレミアム化)とブランド認知を高めます。例えば、空のボトルでラベルがなくても、コカ・コーラのボトルやラムネの瓶を簡単に見分けることができるでしょう。
ガラス製造のトレンド:品質管理の向上
ガラス容器メーカーは、スクラップ部品を減らし、顧客のクレームにつながる問題を回避する目的で、生産の品質に力を入れるようになっています。
品質管理は、ガラスの製造工程のできるだけ早い段階で予測し、必要な措置をすぐに行うことを目的としています。
容器の底部、胴部、首部、仕上げ部の欠陥検査を、主に非接触技術(カメラなどの光学センサー)を用いたインライン検査機で生産全体において行います。
寸法管理は、生産ラインの近くで、通り/止まりゲージを使用、または品質管理室の手動ゲージまたは半自動/自動測定システムを使用してサンプルベースで実行されます。
ガラス容器に求められる寸法管理は以下の通りです。
- 全高
- 垂直性
- 口元の平行度
- 胴体の外径や長辺/短辺、対角線
- 首元の外径
- あらゆる種類の仕上げに関する多くの異なるパラメータ(直径、高さ、半径、角度など)
通り/止まりゲージを使用した管理には、定量的な情報がまったく得られず、オペレーターのスキルに依存するという問題があります。さらに、生産される製品ごとに専用の通り/止まりゲージのセットが必要であり、これらのハード・ゲージを管理し、定期的に再校正する必要があることから、高いコストがかかります。さらに、この方法では、データを収集して統計分析を行いプロセスを改善することはできません。
半自動測定システムは、接触式または光学式の技術に基づいています。測定される容器は手動で搬出/搬入され、測定サイクルが自動的に実行されます。光学技術に基づくシステムは柔軟性に富み、サイズ、形状、色に関係なく、作業を変更することなくさまざまな製品を測定することができます。
自動計測システムでは、容器の取り扱いと測定は、人の手を介入せずに完全に自動で実行されます。それらは主に非接触技術に基づいており、外形寸法に加えて、口元の内径とプロファイル、ガラス壁の厚さ、重量、瓶底の厚み、ラベル貼付領域のプロファイルなどの他の主要点も測定できます。
自動計測システムの利点は、半自動システムと比較し、人件費を大幅に削減できることです。
半自動および自動測定システムで実行された測定結果は、MES (製造実行ソフトウェア) に送信され、管理者がリアルタイムで製造プロセスを微調整および監視するために使用されます。
品質管理室で、ガラス容器をサンプルベースで管理・テストの内容には、次のようなものがあります。
- 衝撃試験
- 垂直荷重
- 内圧試験
- 内容積測定
- 残留ストレス
ガラス容器測定のためのマーポスソリューションはこちらから