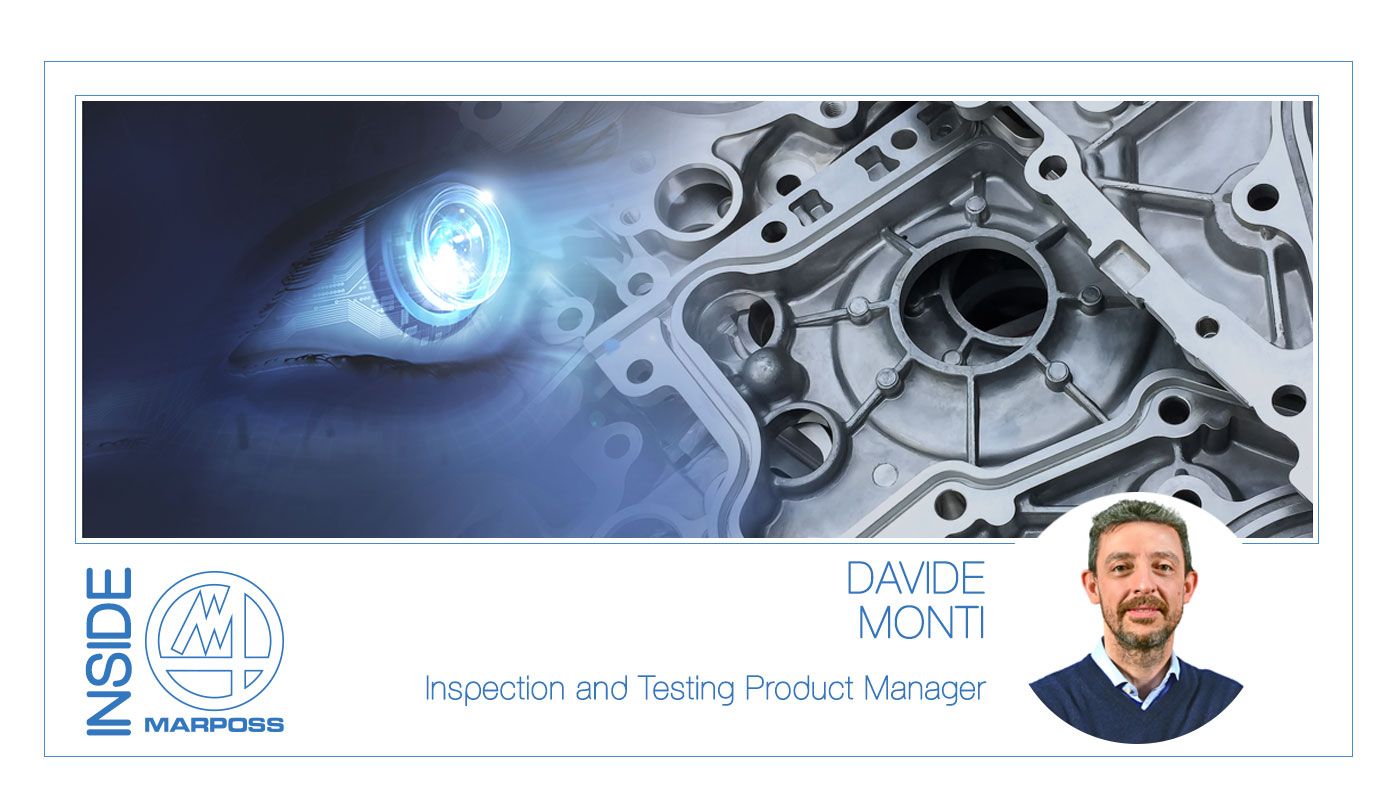
The presence of defects on sealing surfaces, such as porosity, can cause leaks that compromise the correct functioning of the component and jeopardize the life of finished products: the presence of defects on those surfaces may impede the function of the gasket between the mating surfaces by leaving channels free for the passage of fluids.
Checking for the presence of surface defects on cast flat couplings is crucial as it allows to analyze the state of the surfaces on which the sealing gaskets will be applied between different components.
Regardless of the production process, the coupling of the surfaces whose sealing must be guaranteed is carried out by two different processes: the leak test to verify the presence of micro-defects in the structure of the component and the verification of the sealing surfaces to ensure the proper functioning of the existing gaskets.
The right eyes to check for defect
The use of vision systems for surface defect inspection comes from the lack of reliability of surface inspection by operators.
It is well known that human attention to repetitive work tends to decrease in a short period, and as the shift progresses, the likelihood of failing to detect critical defects increases.
The use of automated vision systems eliminates the problem of attention and subjective judgment, providing reliable and reproducible inspection.
For the detection of flaws, Marposs can provide non-contact vision-based systems both automatic and manual turnkey solutions designed to the specific application needs of the customer.
An automated eye for flaws detection: Marposs non-contact vision-based systems
Marposs optical systems have mainly two categories of application;
- Systems using linear and matrix cameras for geometric measurement of part dimensions;
- Inspection applications for checking the surface quality of inspected parts.
Both types of applications can be fully automatic, semi-automatic or manual loaded designed to meet the customer's production requirements:
Here some practical applications of Marposs non-contact vision-based systems.
Non-contact vision-based systems application: dimensional control on hairpin
The hairpin is inherently weak because it consists of a thin copper rod. The use of reference jigs means that the geometry of the part to be measured is affected by the jig itself. The use of contact probes can cause even slight deformation of the part to be measured.
Both result in measuring the part in conditions that are not the real ones.
The measuring system with artificial vision techniques allows to perform the measurement of the part in the absence of deformations induced by the measuring system itself.
Using a vision system for the non-contact measurement of hairpins results in two main benefits:
- the flexibility that the system allows when faced with the great variability of part geometries within the same hairpin family;
- the speed of execution of the measurements as the acquisition of images and the relative processing allows to carry out dozens of measurements on a single component in a very short time.
The measurement is therefore fast and precise.
Non-contact vision-based systems application: inspection of SOFC Semi-cell
Fuel cells convert the chemical energy of a fuel gas directly into electrical energy and can therefore be considered environmentally clean. In addition, because of their high operating temperature, SOFCs are ideal for cogeneration systems with high efficiency up to 90% that can be used to power for instance residential buildings using gases from biomass waste from human consumption.
Dozens of academic studies show the advantages SOFCs in terms of environmental sustainability, and all of them underline how the high operating temperature can be an advantage (cogeneration) but also a disadvantage because it requires the use of noble and faultless materials.
... That is why it is important to test its parts
Anodes and cathodes - the main components of SOFCs - are exposed to enormous thermal and mechanical stresses, and the presence of even small defects in the material can lead to material failure and compromise the proper functioning of the entire fuel cell.
The need for defect-free components requires the use of a system capable of detecting defects characteristic of these types of components (porosity, scratches, depressions, and the general presence of contaminants such as granules). This can be achieved using high-resolution cameras and grazing lights combined with stereo photometric technique.
Non-contact system based on Focault currents: Non-destructive material integrity testing
Marposs offers a solution to find surface faults - such as cracks, porosity, blowholes, inclusions, stripping, etc - without changing the physical state of the part directly on the production line.
Non-destructive material integrity testing has been part of Marposs’ inspection portfolio for over 40 years. It consists of checking surface defects - such as cracks, pores, casting blowholes - using technology known as eddy currents or Foucault currents.
This technology can be easily automated and allows the inspection of all surfaces of revolution such as crankshaft pins and columns, camshaft cams, bearings, hubs, brake discs and in general all parts that demand the absence of structural defects that could compromise the quality and safety of the finished product.
Discover more about Marposs Optical Inspection Systems for the detection of flaws on casted parts