Grinders
Depending on the type of grinder, Marposs proposes different applications:
- in-process and post-process measuring systems,
- wheel balancers,
- monitoring sensors,
- probes
not only to new machines, but also in case of retrofit of used machines.
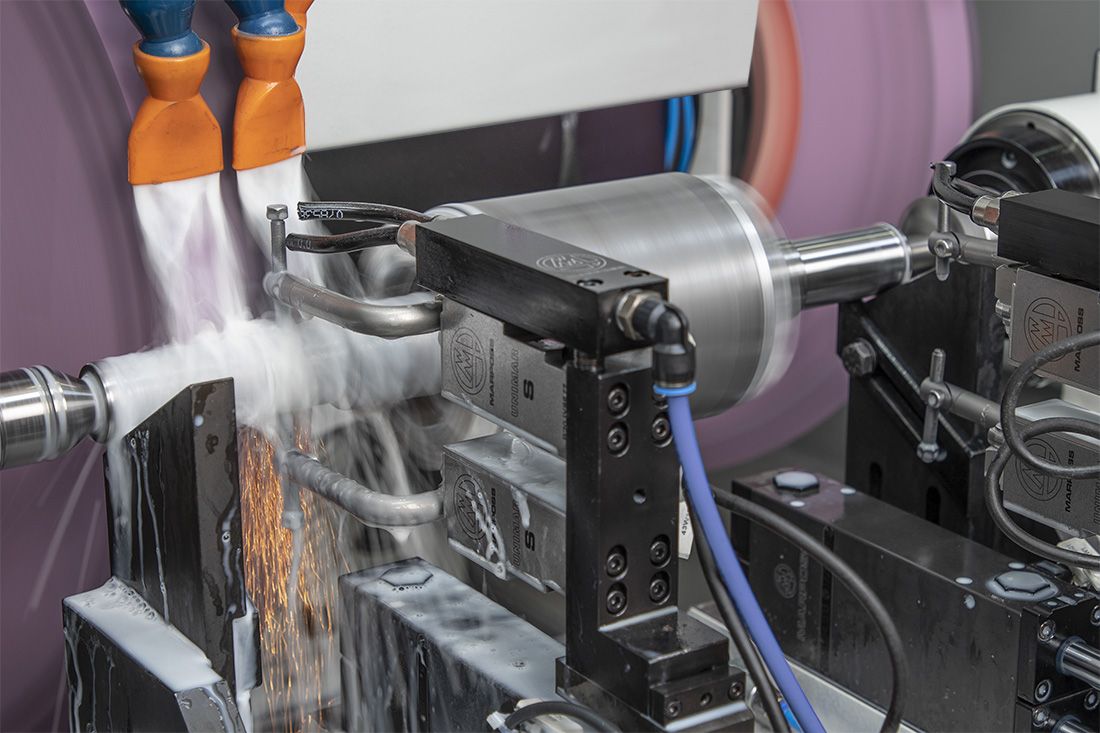
Find your solution
Download
BROCHURES AND MANUALS
Brochure | |
---|---|
English |
Retrofit: (527.58kB)
GRINDIND LINE: (1.16MB) |
Italian |
Retrofit: (531.49kB)
GRINDIND LINE: (1.14MB) |
German |
GRINDIND LINE: (1.14MB)
Retrofit: (534.65kB) |
French |
Retrofit: (531.29kB)
GRINDIND LINE: (1.14MB) |
Spanish |
Retrofit: (531.96kB)
GRINDIND LINE: (1.09MB) |
Czech |
GRINDIND LINE: (1.06MB)
|
Portoguese |
Retrofit: (527.49kB)
|
Japanese |
Retrofit: (580.88kB)
GRINDIND LINE: (1.51MB) |
Korean |
Retrofit: (600.00kB)
|
Simplified Chinese |
Retrofit: (553.59kB)
GRINDIND LINE: (8.15MB) |