The importance of process data collection to improve the quality of the manufacturing process
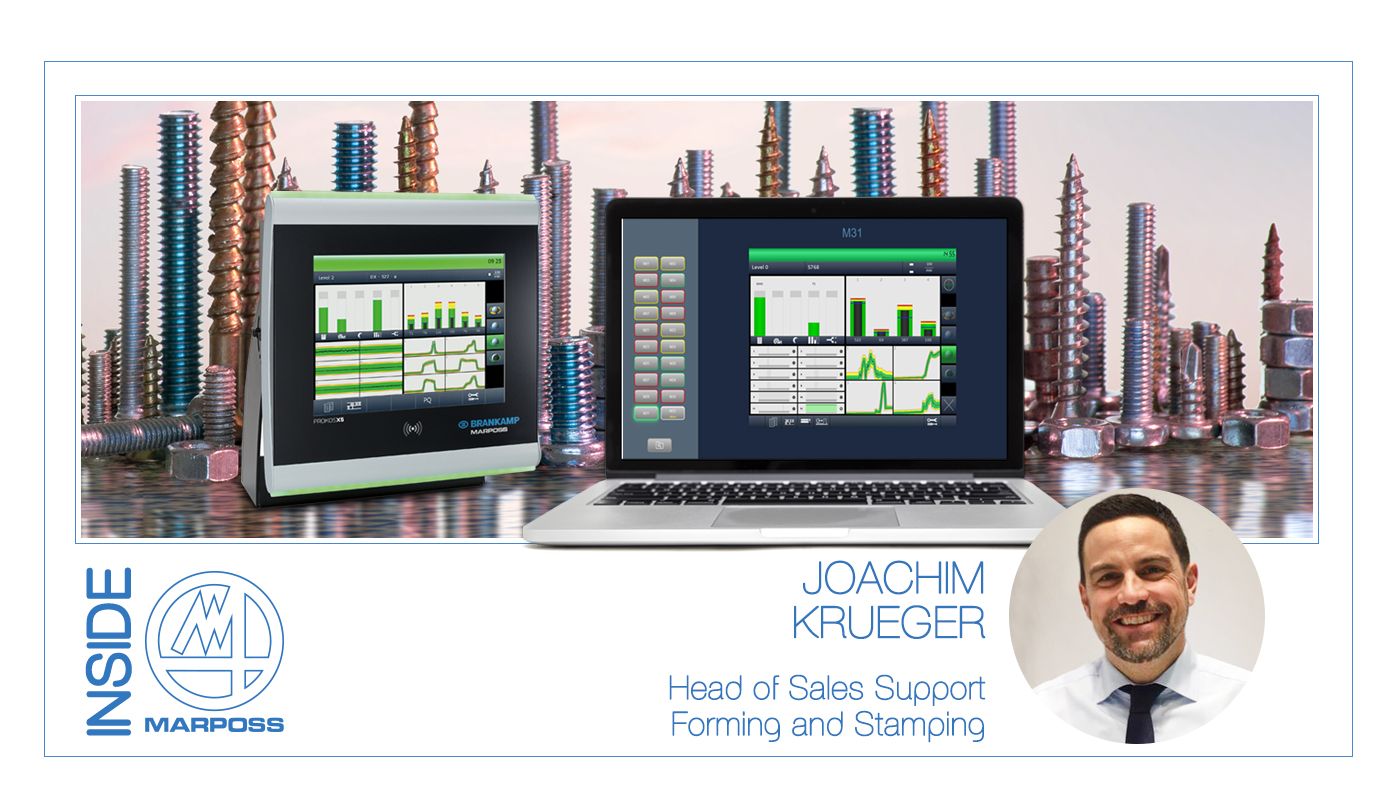
Over the years, manufacturing industries have implemented several process improvements in order to guarantee high quality products and reduce costs, but there is still room for improvement. A huge potential is represented by process data collection.
Industries, such as aerospace or automotive, are realising the importance of data collection to improve operational efficiency. The process data, in fact, provides customers with highly effective tools in evaluation options and traceability, especially when it comes to forming and stamping technology of high-quality parts.
Process data collection during the manufacturing process offers insights that can significantly help to detect faults, which can be analysed precisely. What is more, the exact cause of the faults can be found even after a prolonged length of time . As a result, manufacturers are shifting their focus to a continuous process data collection and the demand for monitoring devices for high-quality requirements is increasing.
The purpose of data collection
By regularly storing the process data with date and time, manufacturers have easier access to information about how the production process is running: force signals and related envelope curves can be transmitted via a network and can be stored automatically so that data is available to users for immediate analysis, or for assessment later in case of customer complaints or for internal analysis in order to evaluate where improvements need to be made.
Marposs Brankamp: the innovative technology for continuous process data collection
Marposs Brankamp offers innovative technologies for real-time monitoring on forming, stamping and assembly machines. Decades of experience as the market leader of process monitoring, are embodied into the systems which guarantee part quality, productivity improvements and the reduction of production costs.
Brankamp systems provide all relevant information for data collection systems and can be easily integrated into Industry4.0 equipment; sensors that are mounted close to the machines and tools record all process-relevant data.
The online access to each monitoring unit enables a powerful tool to have a clear frame of the global production situation, by giving access to the current production situation of each machine, the setting of the monitoring limits and the stability and productivity of the process.
The benefits of Brankamp: to prevent…
One of the biggest challenges in process data collection is finding a way to take raw data, aggregate this data, and then analyze it to reveal critical insights.
With the Brankamp tuning board, selected process data of the monitoring device of each machine are displayed. Parameters such as envelope curve limits, process stability and produced scrap indicate the current status of the process. This process data can be summarized and displayed for immediate indication on the shop floor.
Likewise, in the XViewer, the data can be displayed later and remain available for offline analysis, recall and evaluation, even weeks later. The data can also be used to analyze a trend over the entire production period of a tool, for example over 1 million strokes.
… to correct
Warranty concerns represent another challenge for manufacturers. In fact, the insight into the process parameters during production is lost after a prolonged length of time.
With continuous process data collection, the gap between the regular SPC controls can be closed and conclusions can be drawn about the type or the origin of the faults.
Via the XBrowser of the Brankamp, the files are stored locally on a customer server so that it could be easy to detect the exact cause of a fault in the event of process faults or in-time or stroke intervals.
Discover Marposs’ Brankamp and the benefits of data-driven manufacturing