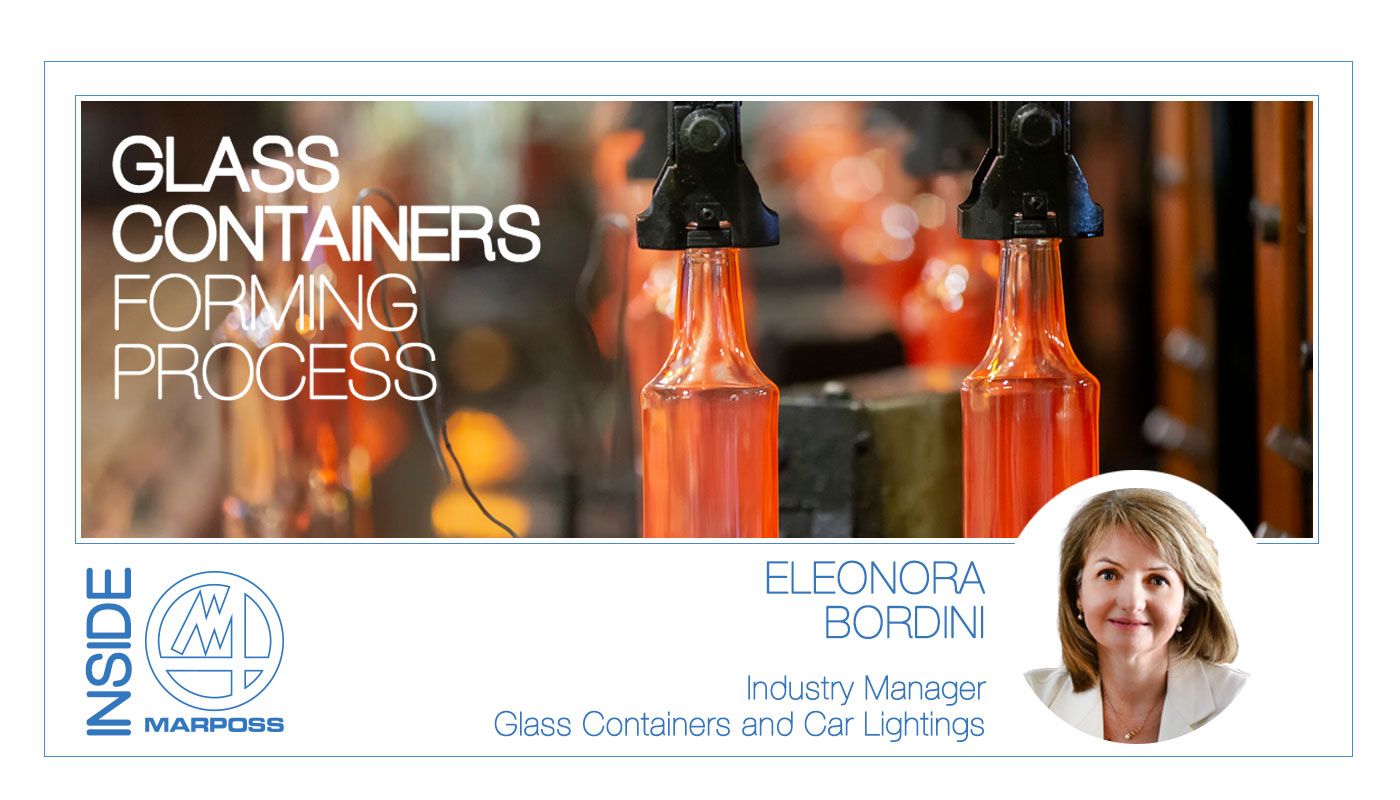
글라스 제조의 발전
유리는 가장 오래된 물질 중 하나입니다. 유리의 역사는 기원전 3500년으로 거슬러 올라가며, 최초의 속이 빈 유리 용기는 이집트인에 의하여 기원전 1500년에 제조되었습니다.
기원전 1세기에 송풍관이 발명되었을 때 기술혁명이 일어났습니다. 이후 진정한 혁명은 20세기 초에 미국에서 마이클 오웬스가 최초로 발명한 중풍 성형기로 이루어 졌습니다. 이를 통해 시간당 최대 2.500개의 글라스 컨테이너를 제조할 수 있어 양산 규모로 생산이 가능해졌습니다.
이 기술은 1925년에 Blow & Blow 또는 Press & Blow 기술을 사용하는 최초의 IS(Individual Sections)기계로 더욱 향상되었으며 오늘날에도 여전히 적용되고 있습니다. 모든 섹션에서 하나 이상의 컨테이너를 독립적으로 생산합니다. 용융된 유리 고브가 비어있는 금형에 떨어지고, 금형은 기법에 따라 미리 부풀려지거나 플런저로 눌려집니다. 미리 성형된 고브는 송풍이 완료된 최종 금형으로 이동됩니다.
최근의 성형기는 최대 20개의 개별 섹션을 가질 수 있으며, 각 섹션은 1~4개의 컨테이너를 동시에 생산할 수 있습니다. 즉, 1 ~ 4개의 용융된 고브(SG = 단일 고브, DG = 이중 고브, TG 삼중 고브, GD = 사중 고브)가 각 섹션에 있는 1-4 개의 금형에 떨어집니다. 이는 각 섹션에서 동시에 일어나며, 컨테이너의 크기와 모양에 따라 생산 속도가 최대 분당 700컨테이너까지 빨라질 수 있습니다.
글라스 컨테이너 : 특성과 장점
글라스 컨테이너는 다음과 같은 다양한 산업분야의 포장재로 사용됩니다:
- 식품 과 음료
- 향수 및 화장품
- 의약품
유리는 비활성입니다: 유리에서 제품으로 아무것도 통과하지 않으며, 외부에서 유리를 통해 제품으로 침투하는 것도 없습니다.
유리는 환경 파괴 없이 지속 사용 가능합니다 (100% 재활용 가능).
유리는 플라스틱 및 알루미늄과 같은 다른 포장재에 비해 아름답고 제품의 가치와 품질을 향상 시킵니다.
한편 유리는 다른 재질에 비해 훨씬 무겁습니다. 지난 몇 년 동안 경량 컨테이너를 얻기 위해 제조 공정이 개선되어 왔으며 이제 20년 전에 비해 최대 40% 정도 가벼워졌습니다. 무게 감량은 운송비 절감 뿐만 아니라 무엇보다 원자재 및 에너지 절약을 위한 필수 요소입니다.
에너지 소비와 이산화탄소 배출량을 줄이기 위해 용해로에서도 상당한 기술 개선이 이루어졌습니다.
글라스 컨테이너의 모양은 점점 더 복잡해 졌습니다. 독특한 형상은 제품 가치(프리미엄화)와 브랜드 인지도를 높일 수 있습니다. 예를 들어, 컨테이너가 비어 있고 레이블이 없는 경우에도 코카콜라 병이나 누텔라 병을 식별하는 것이 얼마나 쉬운지 알 수 있습니다.
글라스 제조 트렌드 : 품질 관리 증진
유리 용기 제조업체들은 불량품을 줄이고 고객의 불만과 관련된 문제를 피하기 위해 생산 품질에도 점점 더 집중하고 있습니다..
품질 관리는 필요한 조치를 즉각적으로 취할 수 있도록 가능한 생산 공정의 가장 빠른 단계에서 이루어져야 합니다.
카메라 및 기타 광학 센서의 비접촉 기술을 기반으로 하는 인라인 검사 장비를 사용하여 컨테이너의 바닥, 바디, 입구 및 표면 마감에 대한 결함 검사가 전체 생산 공정에서 수행됩니다.
치수 관리는 샘플 측정 베이스로 생산 라인 부근에서 한계게이지 또는 QC 측정실의 수동 혹은 자동/반자동 측정기로 수행됩니다.
글라스 컨테이너에 필요한 치수 관리 항목은 다음과 같습니다:
- 전장
- 직각도
- 구부 평행도
- 바디 대각, 장단 혹은 외경 치구
- 목부분 외경
- 마감에 관련된 다양한 항목 (e.g. 직경, 높이, 반경, 각도 등 …) on any kind of finish
한계 게이지를 통한 측정은 합부 판정만을 얻을 수 있으며, 치수값 정보를 제공하지 않으며 더욱이 작업자의 숙련도에 영향을 받습니다. 또한 각 생산 제품마다 전용 게이지가 필요하고, 게이지를 관리하고 주기적인 검교정이 필요하기 때문에 상당한 관리 비용도 소요됩니다. 또한 한계게이지를 통하여서는 프로세스 개선을 위한 측정 데이터의 수집 및 통계 분석이 불가 합니다.
접촉식 혹은 광학기술 기반의 반자동 게이지 시스템이 가능합니다. 측정 대상 소재는 수동으로 로딩/언로딩하고, 측정은 자동으로 실시합니다. 광학 기술 기반의 시스템은 유연한 측정이 가능하며, 별도의 추가 작업 없이 크기, 모양 그리고 색상에 관계 없이 다양한 소재를 측정할 수 있습니다.
자동 측정 시스템에서는 작업자의 개입 없이 컨테이너 핸들링 및 측정을 자동으로 수행할 수 있습니다. 비접촉 기술을 기반으로, 외관 치수뿐만 아니라 구부 내경, 프로파일, 벽두께, 중량, 푸시업 그리고 라벨링 영역의 프로파일 형상등 다른 항목들도 측정 가능합니다.
반자동 시스템과 비교하여, 자동 측정 시스템의 장점은 인건비를 획기적으로 절감할 수 있다는 것입니다.
반자동 및 자동 측정 시스템으로 얻어진 측정결과는 MES로 전송되어 최종 결정자가 제조 공정을 실시간 모니터링 및 관리하는데 사용됩니다.
QC측정실에서 샘플 측정 기반으로 실시되는 글라스 컨테이너의 검사 및 관리 항목은 다음과 같습니다:
- 충격 테스트
- 수직 부하 테스트
- 내부 압력 테스트
- 내부 체적 측정
- 잔류 응력 테스트
유리 용기 측정을 위한 마르포스의 완벽한 솔루션에 대해 자세히 알아보기