下一代压铸生产中的温度控制
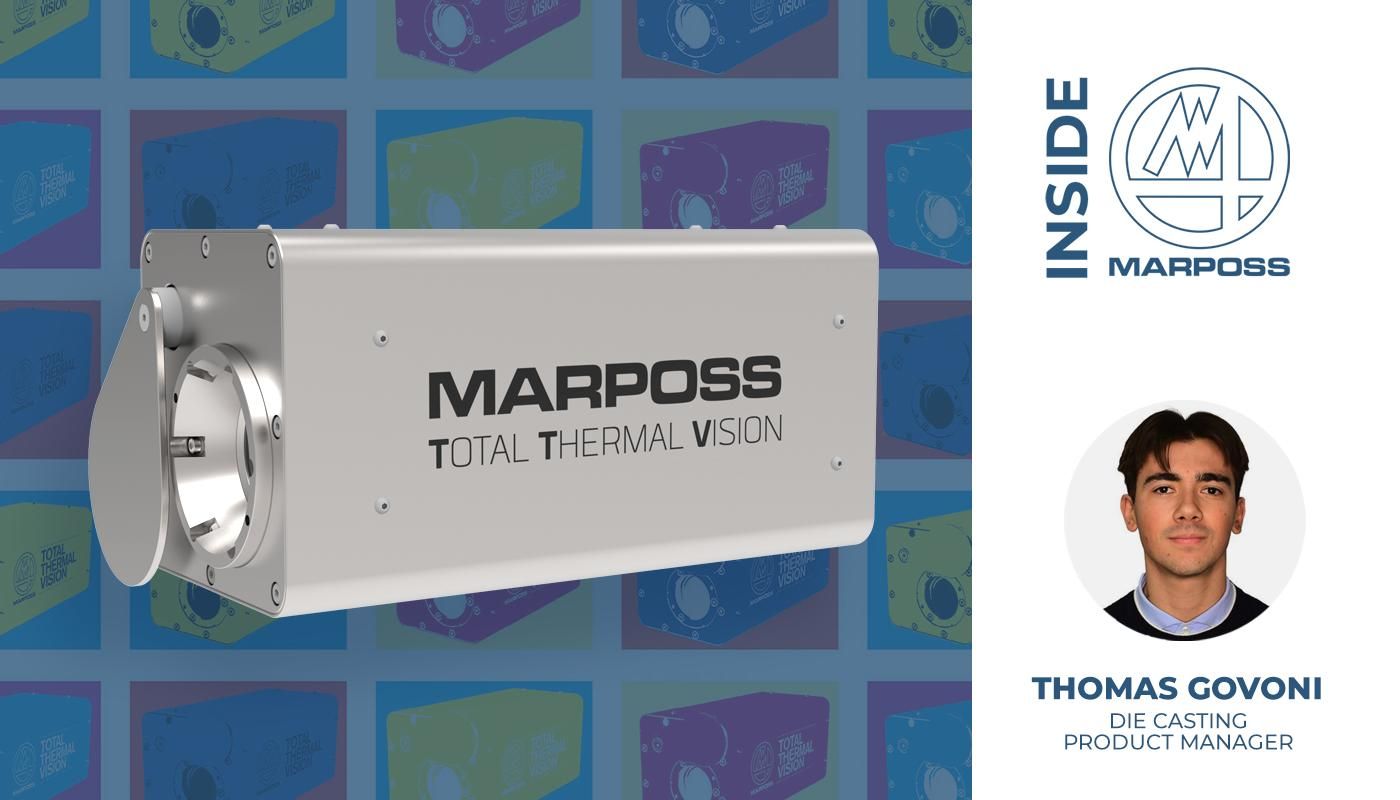
压铸工艺正在快速、深刻地改变工业化生产的面貌,压铸工艺可以生产轻量化、高耐用性和高度复杂的零部件。高压压铸(HPDC)、低压压铸(LPDC)和重力压铸(GDC)技术不断进步,现在可以生产超薄壁厚的工件,壁厚可达0.75 mm,且不影响结构的完整性。在汽车、航空航天和消费电子等行业中,产品减重需求不断增加,压铸技术在工业生产中日渐重要。
2023年,全球压铸市场的规模大约为1,000亿美元,预计到2028年将达到1,400亿美元。这是因为市场需要多样化的解决方案,以达到高效率,从而支持先进材料,同时完成整合数字化与数据采集功能。如今,智能化的压铸设备提供实时监控、预防性维护和工艺控制优化的功能,以实现高效率生产和达到高质量。
压铸技术发展的典型代表是一体化压铸(Gigacasting)技术,其锁模力最高可达20,000吨,为汽车制造带来革命性的变革。其目标是减少零件数,简化装配工艺,在电动车(EV)行业,这是至关重要的因素,以降低生产成本,而成本管控已成为汽车制造商的重大挑战。技术创新、数字化和全新的生产要求显著增加了压铸生产的复杂性。通过现代化的数据采集系统和智能制造技术,制造业正在提高生产效率、产品质量和可持续性。未来几年,压铸行业仍将保持发展,而且可能重塑工业零部件的设计和生产方式。
在压铸过程中,模具的温度控制直接关系到产品质量和模具使用寿命。生产开始前,必须预热每一个模具,以达到理想的温度,避免结构性受损和压铸件缺陷。模具与熔融金属间的显著温度差可导致表面应力,增加模具磨损速度,影响产品质量。相反,保持温度分布均匀可减少热裂纹,进而避免提前失效,例如裂纹或气孔缺陷,因此,可以延长模具使用寿命。如果温度控制不足,常常导致高废品率,进而影响生产效率和设备使用寿命。要实现工件的高表面质量、尺寸精度和达到理想的充模效果,严格控制模具温度平衡至关重要,还可缩短节拍时间并提高成品率。
马波斯第三代模具表面温度监控系统(TTV)是压铸行业温度控制技术重大发展的代表性产品,马波斯以丰富的行业经验和全球300多套装机量,显著提升了该系统的工作性能。多年的事实证明,TTV温度监控系统在高附加值零部件生产中发挥着不可或缺的作用,投资回报期仅数月。得益于其所搭载的高可靠性的热成像相机和先进的软件。下一代产品的模具表面温度测量可以达到更高精度(±2度,而上代产品为±5度),产品质量更高,优化温度控制和喷射阶段。温度监控系统应用效果显著,可降低废品率,提高设备综合效率(OEE),特别适用于现代化大型压铸机和新型一体式压铸机(Gigacasting)。
与此同时,马波斯从2025年开始进一步丰富TTV产品线,提供更多模块化方案,可配不同数量的热成像相机和不同的集成度,更好地适应不同规格产品的压铸生产。为此,马波斯正在开发TTV Light,这是一款简版和经济型温度监控系统,适用于中小型压铸机,尺寸小,机械结构紧凑,性能和质量高且价格诱人。
除机械系统创新外,数字化正成为基础型技术,可以优化生产。温度监控系统集成生产执行系统(MES)和物联网(IoT)后可实时监控生产过程,确保高效率的综合管理。TTV系统采集温度数据,进行生产中分析或生产后分析,支持生产方式的转型。此外,结合人工智能与TTV温度监控系统,可有效降低废品率和提高生产效率,同时降低对压铸机操作员技能的依赖。
可见,马波斯的创新技术将继续引领压铸行业温度监控方案的发展,精准预见有关数字化和人工智能技术应用的市场需求。马波斯致力于提供前沿的监控方案,帮助压铸企业提高生产效率、可持续性并应对未来挑战。