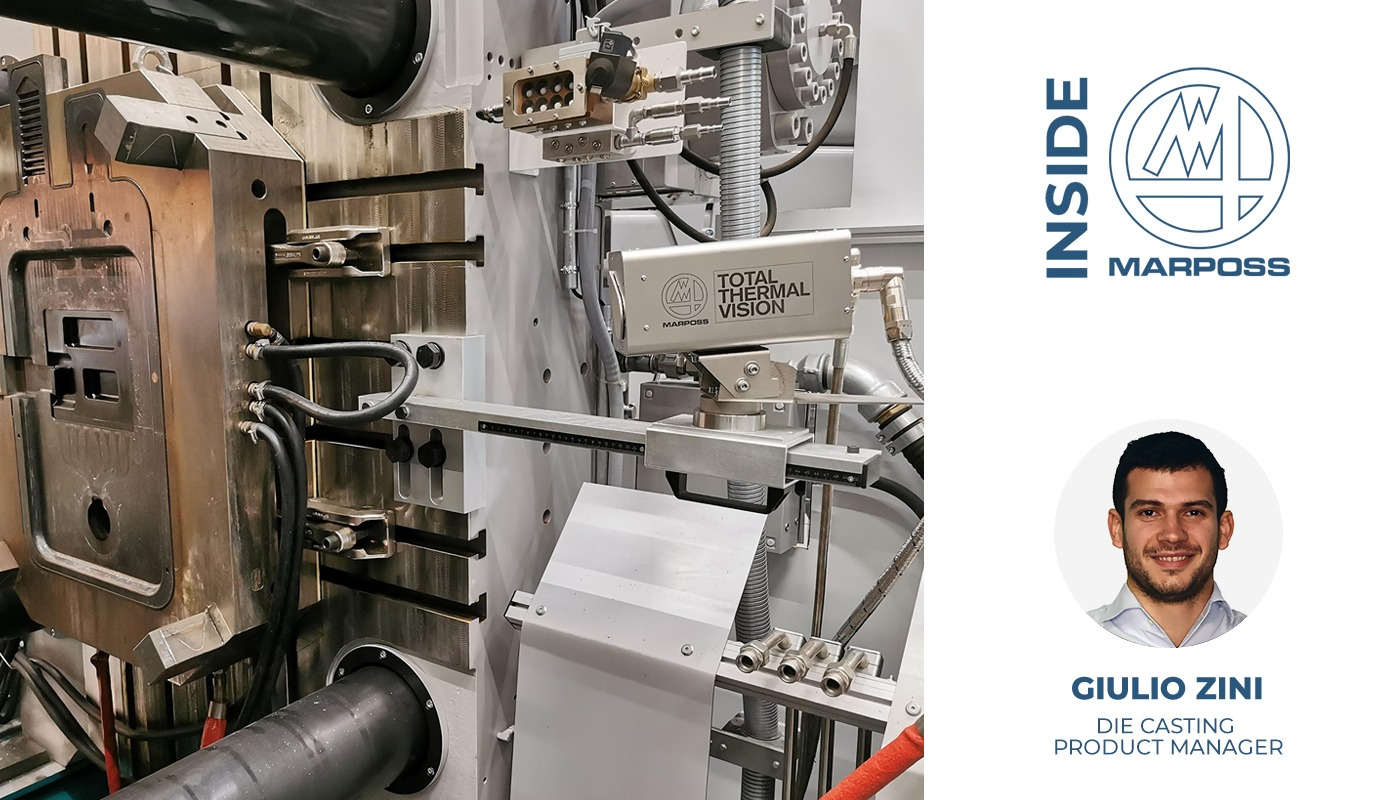
As nations worldwide aim to cut emissions and embrace eco-friendly transportation, the automotive industry faces increasing pressure to reduce vehicle weight and enhance sustainability. This push towards 'lightweighting' is crucial for improving fuel efficiency, range, and emissions in the growing fleet of hybrid and electric vehicles. To achieve this target, engineers are adopting advanced materials like aluminum, necessitating a reevaluation of manufacturing processes and the incorporation of new technologies.
Die Casting Evolution: Shaping the Future of Automotive Manufacturing
A notable shift in focus involves the die casting process, a key manufacturing method in the automotive industry. Traditionally used for components like engine blocks, die casting is now being employed for one-piece structural parts such as shock towers and body parts, aligning with the industry's goal of weight reduction. Some of the major automotive players are pioneering this shift by favoring a single-piece die-cast underbody structure with the use of giga/mega presses, a move that could revolutionize automotive manufacturing.
Heat matters: the crucial Role of thermal factors in Die Casting
Despite the well-known benefits of die casting, such as its quick and cost-effective nature, the move towards larger components introduces complexities: in particular, ensuring quality and cost-effectiveness becomes challenging. In this context, it is crucial to optimize the number of rejects in the process, knowing the myriad parameters that operate simultaneously.
Every process engineer knows that most of the issues are related to thermal reasons. The thermal factors in die casting include the temperature of the alloy used for casting, the temperature of the die itself, and the temperature of the die-casting machine. Each of these must be kept in an optimum temperature range to ensure the highest part quality. For example, if the mold temperature is too cold, the temperature of the metal could drop too quickly as it flows into the mold and cause defects, such as greater porosity or misruns on the casting surface. It is therefore clear that checking the surface temperature of the mold becomes essential.
Efficiency in every shot: TTV minimizes defects and optimizes Die Casting processes
Marposs Total Thermal Vision (TTV) system is designed to effectively assess temperature distribution across the mold surface and indirectly maintain the stability of the process which is influenced by more than 300 parameters.
TTV can continuously monitors die temperature distribution for each shot and, in the event of deviations, it promptly issues alarms to prevent the creation of defective parts. This is performed by a seamlessly integration with the manufacturing cell as part of the 4.0 smart manufacturing environment and without impacting cycle time. TTV enhances the efficiency of the production providing a global improvement to the process. Just to underline some of the benefits, we could mention the reduction of scrap parts, the extension of mold life span, the optimisation of the sprayer action regarding lubricant composition and cycle time duration in High-Pressure Die Casting (HPDC) processes.
The data collected by TTV are stored in several different formats like thermographic images, image formats or text file and can be integrated into the plant's Manufacturing Execution System (MES) for real/off line analysis. All of these improvements are leading to an immediate reduction of operative costs (fast payback) and heightened customer satisfaction in terms of part quality.
What’s new for 2024
From 2024, Marposs is capable to offer systems with eight thermocameras included in the same unit and the capability to detect 40 region of interest (ROI) in the same picture. In this way the entire surface of big and complex molds of giga/mega presses can be checked in one single frame. Furthermore TTV is now available in any kind of hardware configuration, stand alone or completely integrated in the machine.
Given the monthly production volume and the improvements assured by TTV, the return on investment typically is calculated in months and not years. Marposs offers free demonstrations with service personnel, allowing users to experience tangible benefits right from the initial plug-and-play installation, which takes only a few days.
By embracing innovative technologies and solutions, the die casting industry can overcome the challenges associated with casting complex, one-piece structures. As the automotive sector continues its shift towards larger and more intricate die-cast parts, the adoption of a system that checks the surface temperature of the molds becomes imperative for achieving improved efficiency, reduced costs, and minimized environmental impact.
DISCOVER MORE ABOUT TTV