Automatic Line for Prismatic Cells Electrical Testing (EOL)
Marposs offers its competences in measurement and testing, combined with its experience in automated implementations, as turnkey solutions for the evaluation of EV batteries. The portfolio of applications covers the entire production chain of cells, modules and packs.
The solutions proposed can be applied in mass production, for the final quality gate in the manufacturing of cells (End of Line station), as well as for the entry testing and grading of cells in the module assembly line (Beginning of Line station).
These systems can carry out the complete cell characterization; evaluation of the main dimensional parameters through optical or contact gauges, inspection of the surface quality with machine vision technologies and A.I. elaborations and measurement of the electrical characteristics, configurable according to the specific requirements of the customer.
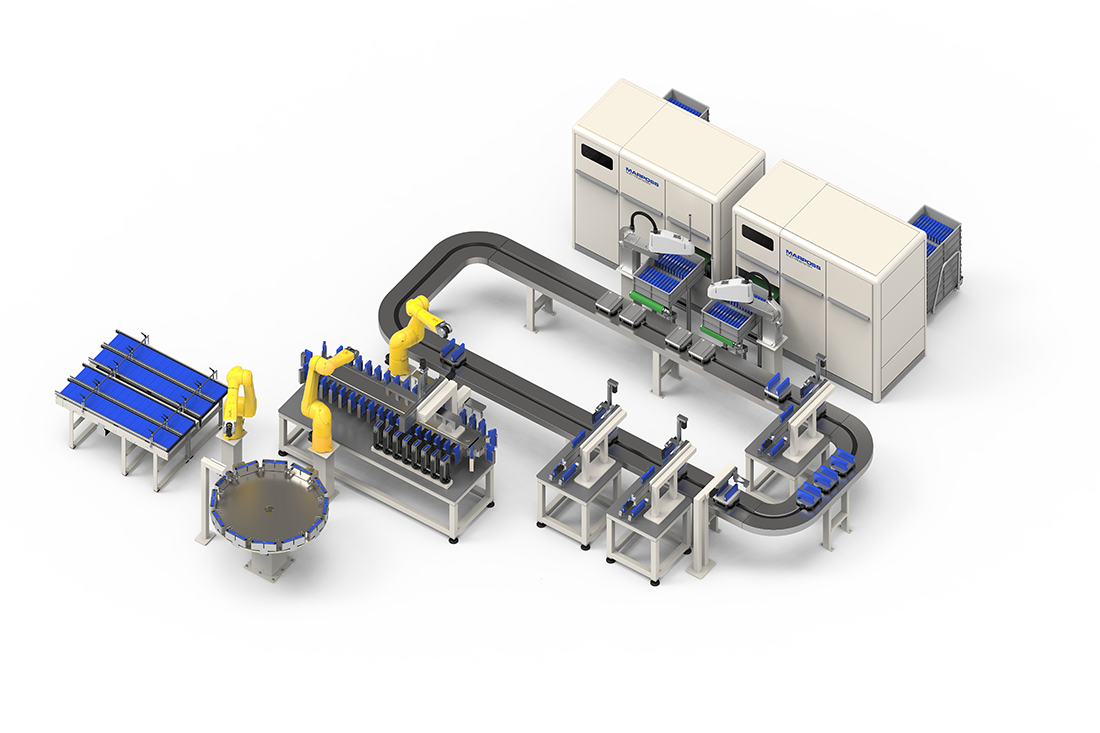
The fully automated machine described is an example of a plant designed to process prismatic cells for the Beginning of Line testing in a Module assembly line.
The cells are fed by means of trays collected in stacked boxes stored in an automatic warehouse. The automation separates each tray so that it can be handled by a robot whose task is to transfer the cells from the warehouse to the pallet conveyor. The required cycle time makes it necessary to have a certain number of warehouses and corresponding robots working in parallel.
The first inspection station consists of three benches equipped with camera systems to check each side of the cell casing for defects and to determine the orientation of the poles. The rejects are segregated; the good ones are placed back on the conveyor pallet with the correct pole orientation, to move on to the next station thanks to a servo-controlled Cartesian manipulator. The number of benches depends on the expected cycle time.
The second test station consists of a turntable with nests where the OCV/DCIR test is performed thanks to pogo-pin probes. Different type of tests can also be performed, depending on customer’s specification. One set of multiple cells is lifted at a time and surrounded by conductive foam to perform electrical insulation tests (Hi-Pot) on all the cells processed in parallel. A robot transfers the cells to and from the current station.
The third measuring station is dedicated to the evaluation of the thickness of the cells thanks to the application of a precise and preset pressure of the contact probes. The nests are distributed on the edge of a circular turntable.
Finally, the successfully inspected cells are sorted on conveyor belts and the rejects are removed. Again, a robot is used to handle the cells.
- Flexibility thanks to:
o A pallet conveyor used as a buffer and to bypass excluded stations
o Changeover of nests and tools to different cell types
o Test parameters and mechanical characteristics that can be set as recipes
- Selectable tests and scalable solution to add more stations/tests or reduce throughput
- Reduced and adaptable footprint according to the specific layout of the assembly workshop
- Manual operations only for loading trays (with special trolleys) and unloading tested cells
- E9066 PC integration for statistical analysis and control charts
- Manual parts handling
- Automatic parts handling
- Optional automatic storage for input cells
- Footprint of configuration shown (HxWxD): 2,500 x 9,000 x 9,000 mm
- Efficiency: 97
- Cycle time: depending on pulse duty cycle